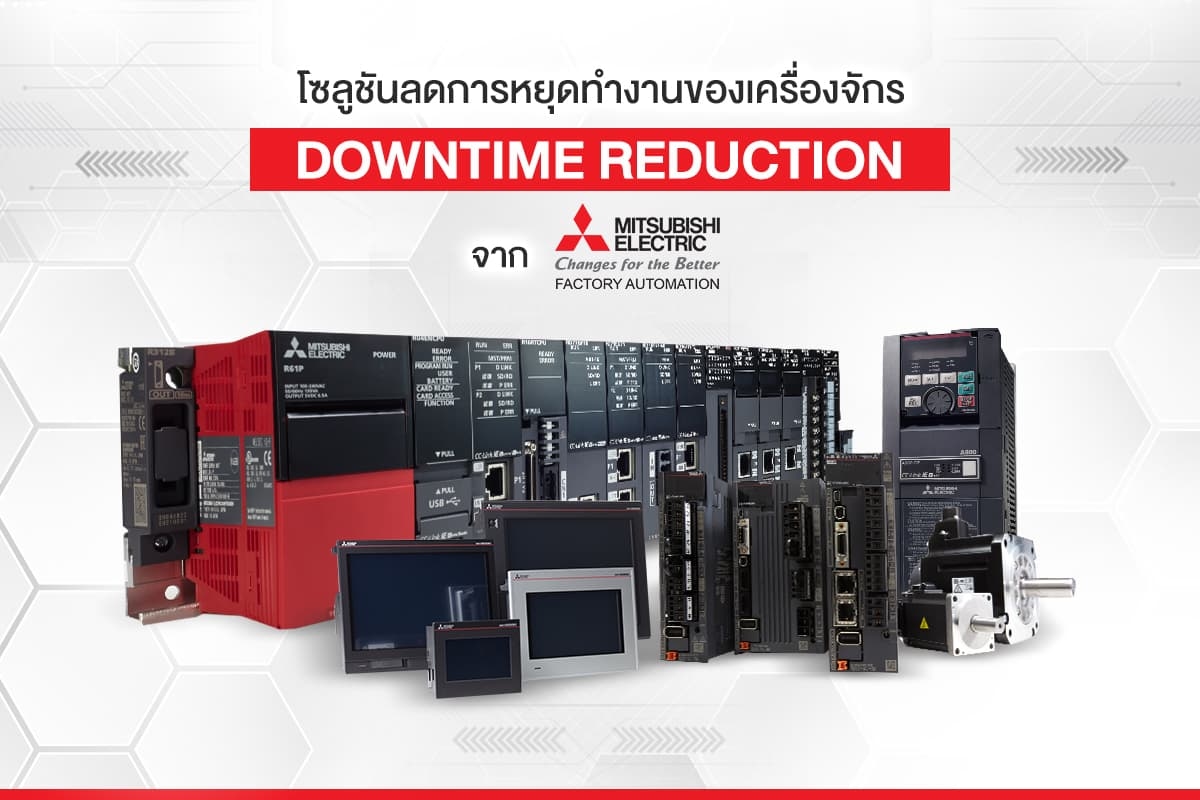
ในการทำงานของภาคอุตสาหกรรม โดยเฉพาะส่วนงานไลน์การผลิต มักจะเกิดปัญหาการหยุดการทำงานของเครื่องจักร (Downtime) ซึ่งมีด้วยกันหลายปัจจัยที่จะทำให้เกิดปัญหาดังกล่าว ซึ่งโซลูชันการแก้ไขปัญหานั้นก็มีด้วยกันหลากหลาย แต่การแก้ไขปัญหาที่ครอบคลุมนั้นก็ยังเป็นเรื่องยากอยู่เสมอ ทำให้ต้องมีการพัฒนาและคิดค้นโซลูชันใหม่ๆ เพื่อแก้ไขปัญหา การหยุดการทำงานของเครื่องจักร (Downtime) ในไลน์การผลิตอยู่ตลอดเวลา
Mitsubishi Electric ได้คิดค้นและพัฒนาฟังก์ชัน ‘Downtime reduction solutions’ ซึ่งเป็นโซลูชันสำหรับลดการหยุดการทำงานของเครื่องจักร (Downtime) ในไลน์การผลิตโดยเฉพาะ โดยแนวคิดในการแก้ไขปัญหาส่วนใหญ่ของไลน์การผลิต ประกอบด้วย 3 ฟังก์ชันหลัก ดังนี้
1. ฟังก์ชันการระบุปัญหาได้อย่างรวดเร็ว
2. ฟังก์ชันการจัดการปัญหาที่ทำได้ง่ายดาย
3. ฟังก์ชันการป้องกันปัญหาที่อาจเกิดขึ้น
โซลูชัน ‘Downtime reduction solutions’ ได้ถูกพัฒนาเพื่อให้สามารถแก้ไขปัญหาได้อย่างครอบคลุม โดยการรวบรวมปัญหาในไลน์การผลิต เพื่อให้สามารถตอบโจทย์การทำงานของไลน์การผลิต ซึ่งจะช่วยให้การทำงานและการผลิตสามารถทำงานได้อย่างมีประสิทธิภาพ ลดการหยุดการทำงานของเครื่องจักร (Downtime) และช่วยให้องค์กรสามารถลดต้นทุนได้ดีขึ้น เนื่องจากลดระยะเวลาในการซ่อมบำรุงออกไปและทำให้ผลผลิตต่อเนื่องมากยิ่งขึ้น
1. ฟังก์ชันการระบุปัญหาได้อย่างรวดเร็ว
■ การตรวจสอบระยะไกล / การบำรุงรักษาระยะไกลของ PLC (ตรวจสอบได้บน PLC)
ด้วยการใช้งานฟังก์ชัน Web Server ใน PLC ของ CPU โดยสามารถตรวจสอบได้ทันที แม้กระทั่งขณะที่เกิดปัญหาขัดข้อง ซึ่งไม่ต้องใช้เครื่องมือหรือโปรแกรมเสริมในการตรวจสอบ นอกจากนี้ผู้ใช้งานสามารถสร้างหน้าเว็บเพิ่มขึ้นเพื่อใช้ตรวจสอบได้อีกด้วย
■ มอนิเตอร์ระยะไกล / บำรุงรักษาระยะไกลบนหน้าจอ Mobile Device (ตรวจสอบได้บน HMI)
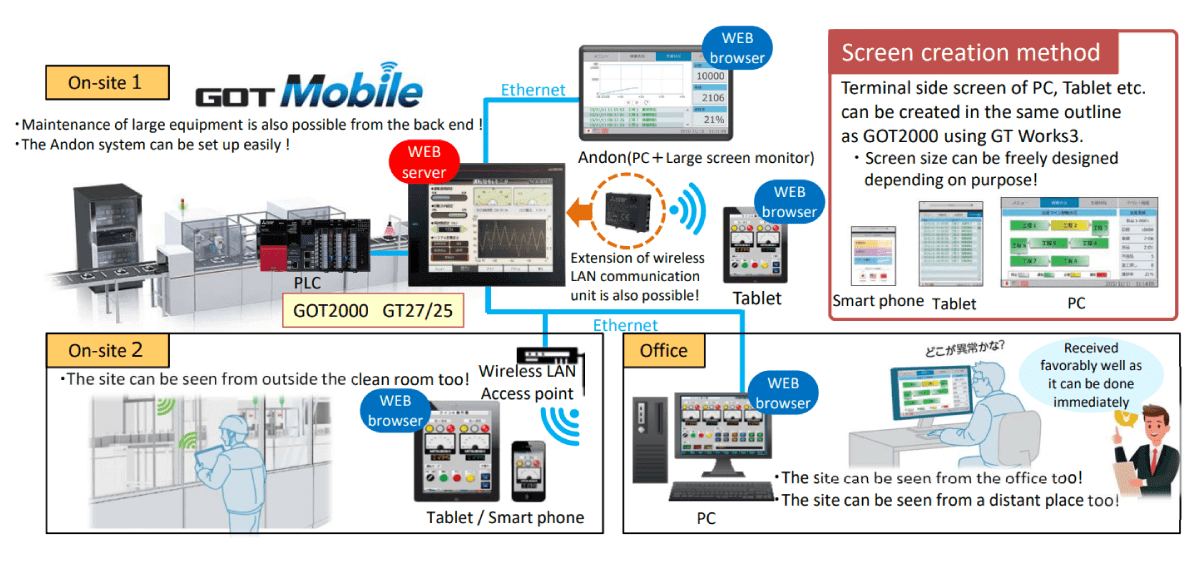
ด้วยการใช้ฟังก์ชัน GOT Mobile ของ GOT2000 ทำให้สามารถตรวจสอบสถานะและตั้งค่าอุปกรณ์จากระยะไกลได้
■ การแจ้งเตือนเมื่อเกิดปัญหา (ตรวจสอบได้บน HMI)
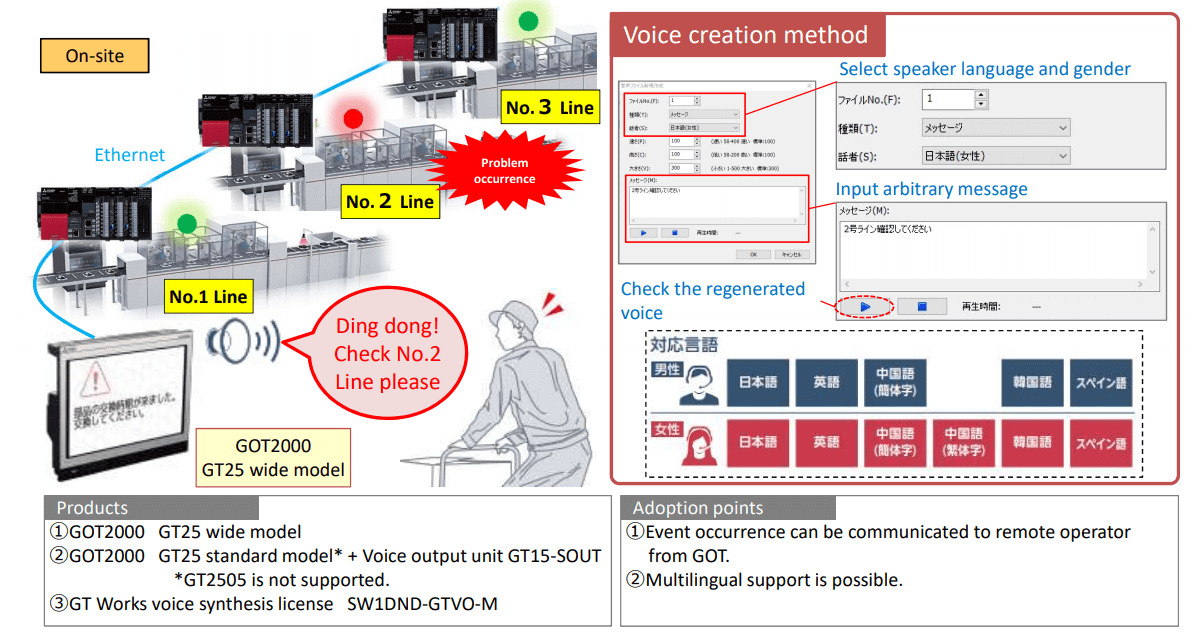
การตั้งค่าแจ้งเตือนเมื่อเกิดปัญหา ใช้งานได้ด้วยฟังก์ชันเอาต์พุตเสียง (Voice Output Function) และฟังก์ชันสังเคราะห์เสียง (Voice Synthesis Function) บนหน้าจอ GOT2000 โดยสามารถตั้งค่าการแจ้งเตือนได้อย่างง่ายดาย ผ่าน ซอฟต์แวร์ GT Works3
■ ระบบตรวจสอบแบบ Wireless และระบบ ANDON (ตรวจสอบได้บน PLC / HMI)
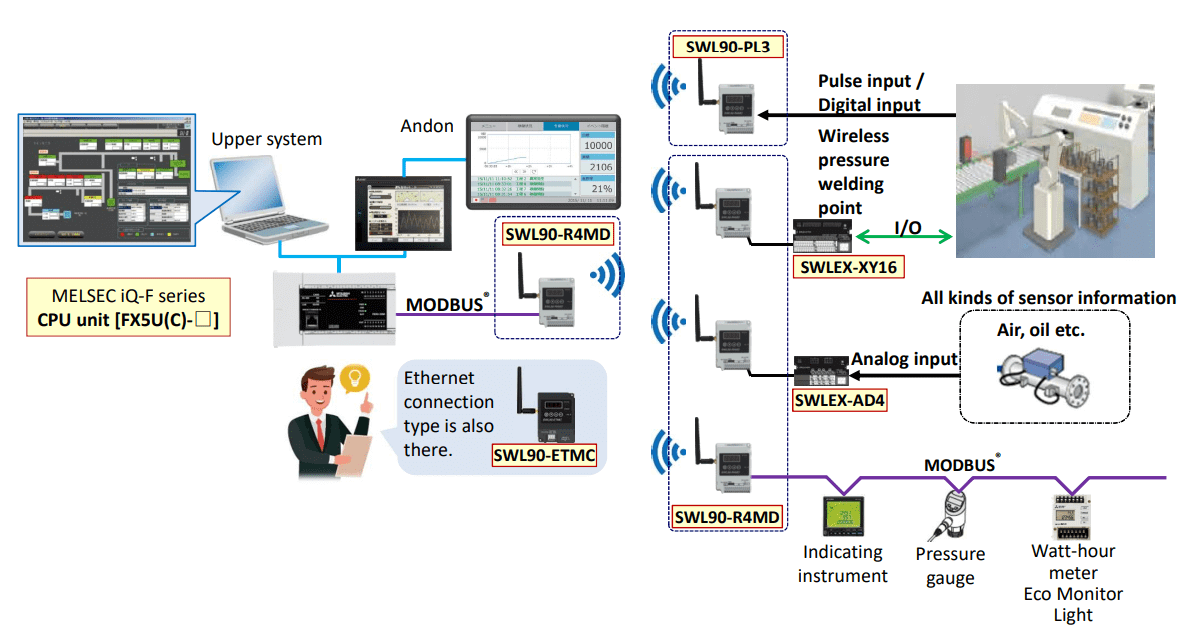
ตรวจสอบด้วยการใช้ชุดอุปกรณ์ Wireless SWL90 series บนความถี่ 920 MHz (อุปกรณ์ของ Mitsubishi Electric System and Service) และระบบ ANDON ของอุปกรณ์ในการตรวจสอบสถานะการติดตั้ง หรือ สถานะการผลิตสัญญาณเตือน ฯลฯ สามารถตั้งค่าได้ผ่าน PLC และ HMI
> Wireless ความถี่ 920MHz แต่ไม่เกิน 2.4GHz
> Sub-station สามารถใช้ relay กับการสื่อสารแบบ multi-hop
> ช่วยลดการเดินสายเคเบิลให้ลดลง และ ปรับแก้ไขได้ง่าย เนื่องจากใช้สายเคเบิลน้อยกว่าปกติ
> สามารถใช้การควบคุมแบบ Wireless กับชุดเคลื่อนที่ เช่น AGV และอื่นๆ
> รองรับการเชื่อมต่อแม้เกิดแผ่นดินไหว หรือ การเคลื่อนย้าย
> สามารถสื่อสารระยะไกลระหว่างชั้น, อาคาร ได้ง่ายดาย
■ ตั้งค่าการตรวจสอบของระดับในการตรวจจับ (Sensing Level) ได้ทันที
ด้วยการใช้เซ็นเซอร์ที่รองรับกับ iQSS สามารถตรวจสอบระดับในการตรวจจับ (สถานะของเซ็นเซอร์) ได้แบบ Real-time บน PLC และ GOT2000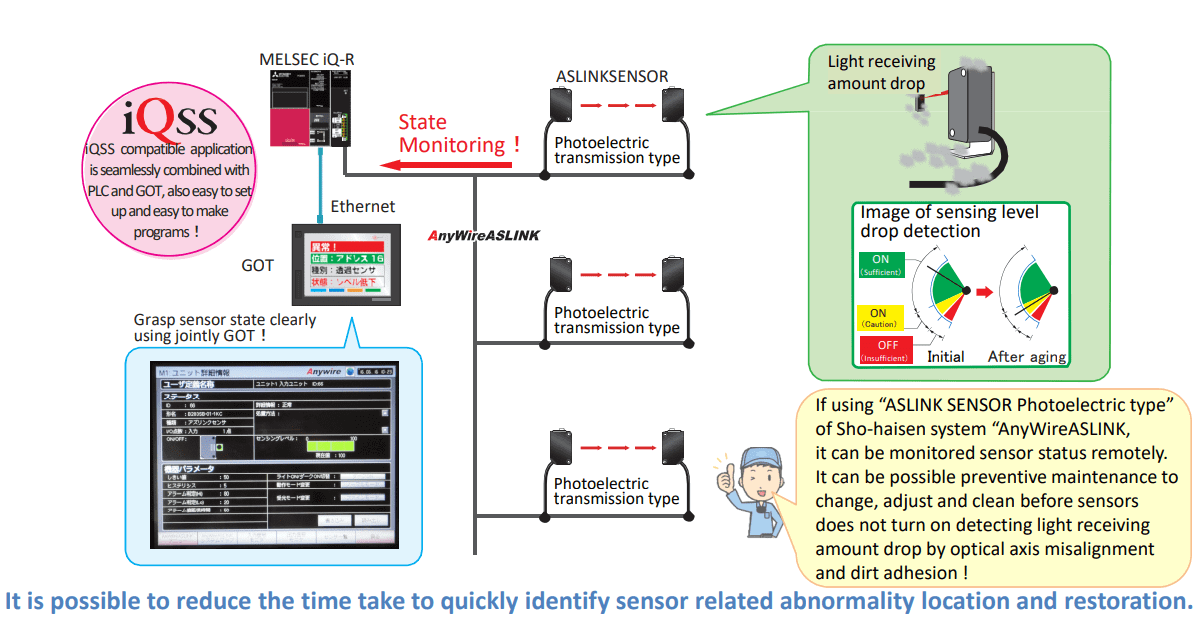
■ ตรวจจับกระแสไฟฟ้าลัดวงจร / การตัดการเชื่อมต่อเซ็นเซอร์ในทันที
ด้วยการใช้เครือข่ายสายไฟขนาดเล็ก AnyWireASLINK สำหรับตัดการเชื่อมต่อกับสายเคเบิลของเซ็นเซอร์หรือเซ็นเซอร์ไฟฟ้าลัดวงจร โดยทำให้ระบบสามารถตรวจจับปัญหาจริงได้แบบ Real-time
1. ตรวจจับเซ็นเซอร์การตัดการเชื่อมต่อกับเคเบิล
2. ตรวจจับเซ็นเซอร์กระแสไฟฟ้าลัดวงจร
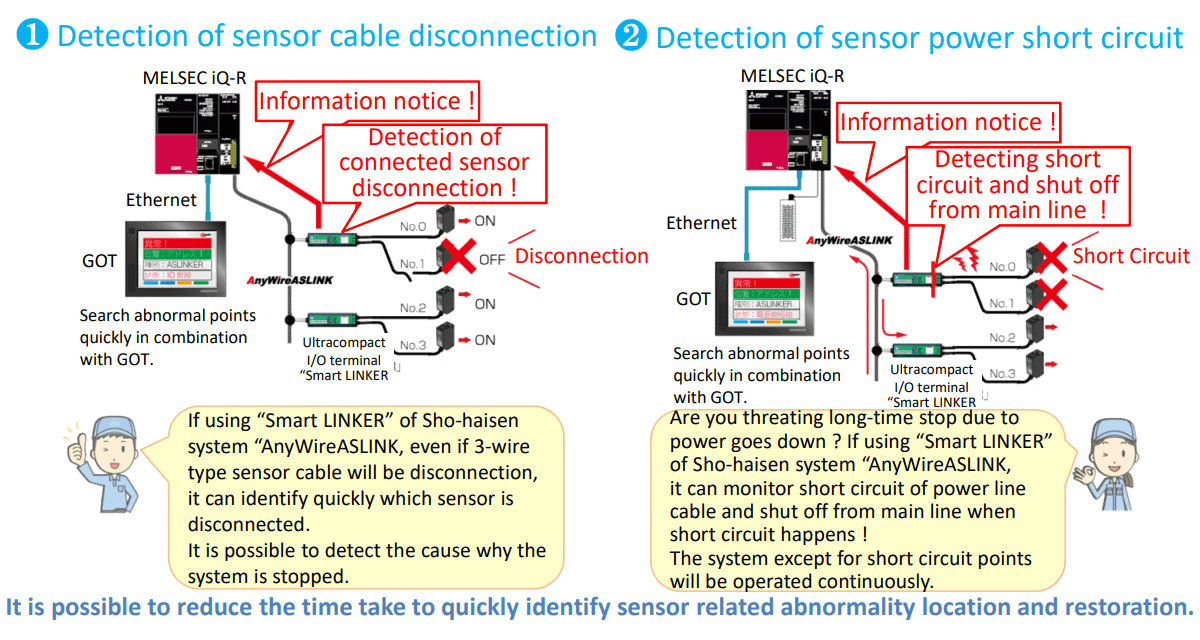
2. ฟังก์ชันการจัดการปัญหาที่ทำได้ง่ายดาย
สำหรับปัญหาในไลน์การผลิต องค์กรอาจเคยพบปัญหาเหล่านี้:
1) เกิดปัญหาเดิมๆ ขึ้นบ่อยครั้ง แต่ไม่สามารถตั้งค่าทำซ้ำเพื่อแก้ไขได้อย่างง่าย
2) ต้องการบันทึกสถานะก่อน-หลัง เพื่อตรวจสอบปัญหา
3) ทราบสาเหตุของปัญหา แต่ไม่มีบันทึกหลักฐาน
4) ตรวจพบความผิดปกติในระบบอุปกรณ์ แต่ไม่สามารถระบุข้อมูลของอุปกรณ์ หรือ การดำเนินการของผู้ปฏิบัติงาน เมื่อเกิดปัญหาขึ้น
■ การติดตั้งและปรับแต่งอุปกรณ์ โดยไม่ต้องเปิดหรือปิดแผงไฟฟ้า
ด้วยการใช้ฟังก์ชัน FA การมองเห็น (FA Transparent Function) ของ GOT2000 โดยสามารถตั้งค่า, ปรับแต่ง หรือ ปรับเปลี่ยนโปรแกรมของผลิตภัณฑ์ FA ผ่าน GOT ได้ แม้ในขณะที่ปิดแผงไฟฟ้าอยู่
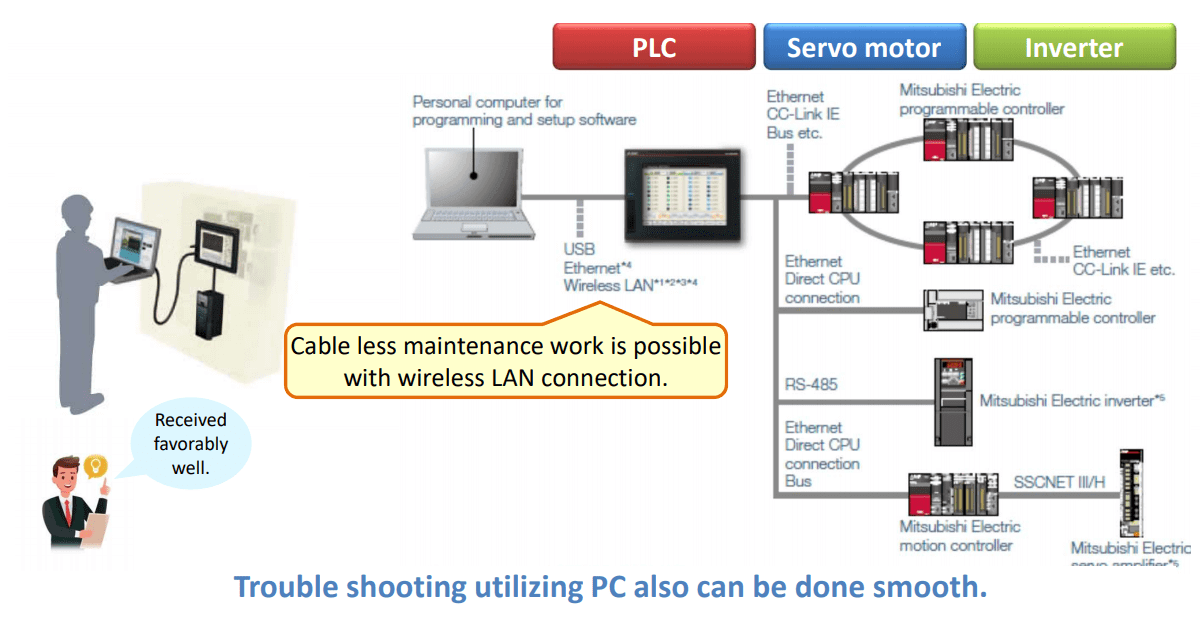
■ การคืนค่าโปรแกรมหรือพารามิเตอร์ (ตรวจสอบได้บน HMI)
การสำรองและกู้คืนโปรแกรม PLC, Inverter และ Servo amplifier ด้วยฟังก์ชันสำรอง /คืนค่าข้อมูล (Back up /Restore Function) ผ่าน GOT2000
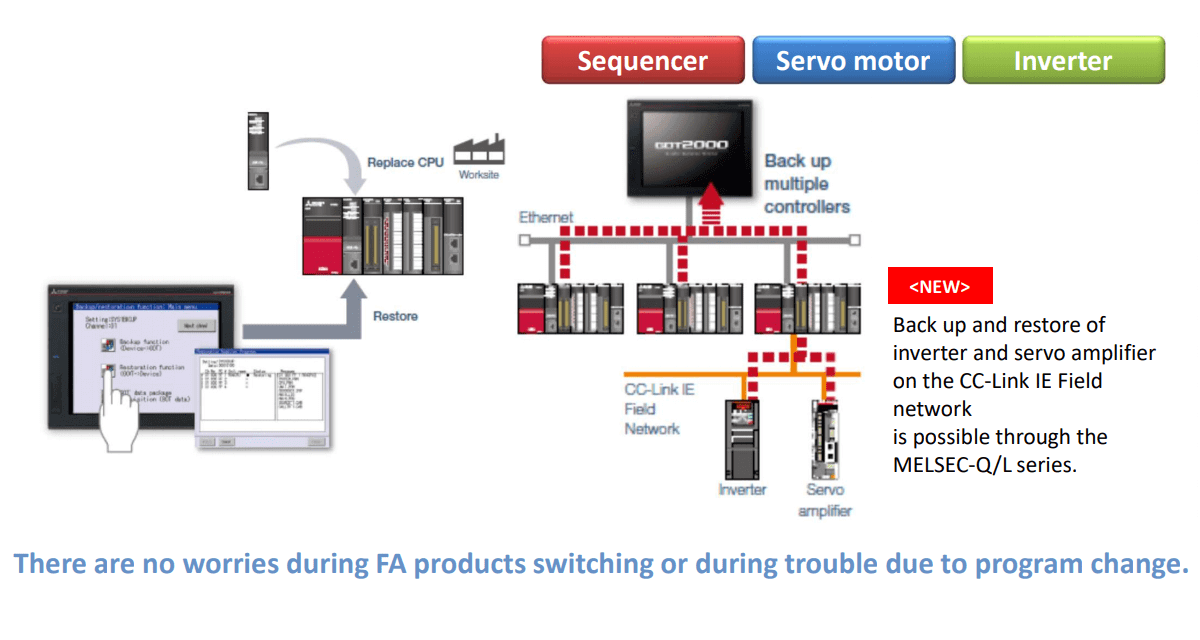
■ การจัดเก็บข้อมูลของอุปกรณ์ เพื่อตรวจสอบความผิดปกติ (ตรวจสอบได้บน PLC / PC)
การจัดเก็บข้อมูลของอุปกรณ์ ด้วยการใช้ฟังก์ชันการถ่ายโอนข้อมูลหน่วยความจำ (Memory Dump Function) ของ PLC CPU ผ่าน SD การ์ดโดยอัตโนมัติ (ตามเงื่อนไขที่กำหนด) ซึ่งจะมีการแสดงข้อมูลสถานะของอุปกรณ์ เพื่อให้สามารถตรวจสอบความผิดปกติของอุปกรณ์ได้ในภายหลัง
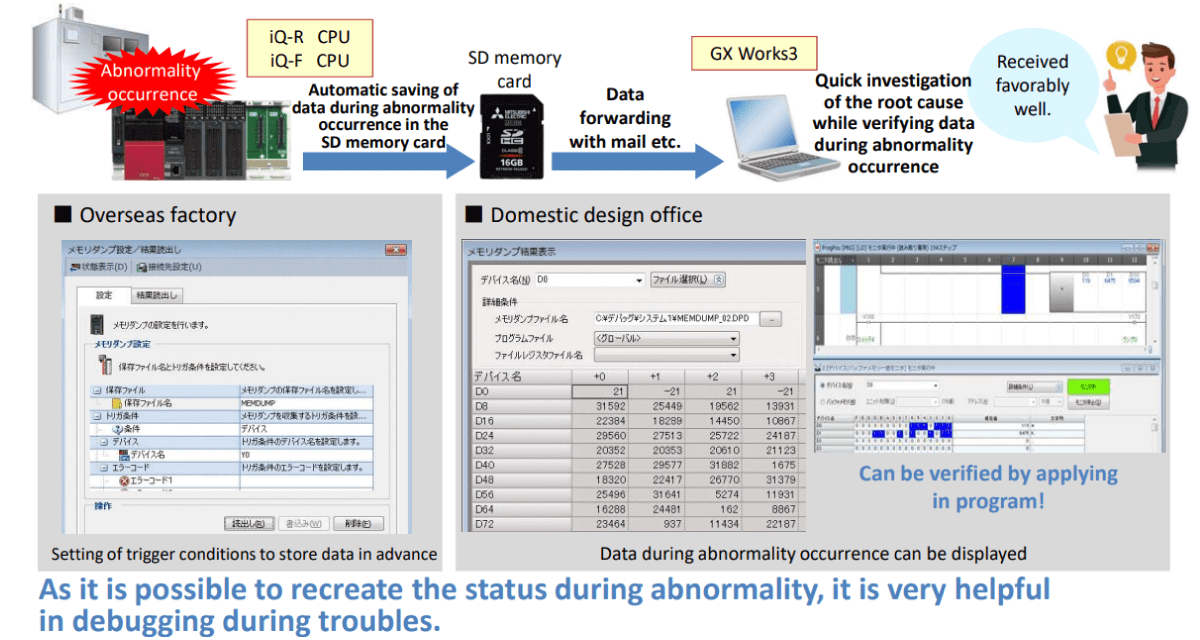
■ จัดเก็บประวัติการทำงาน เพื่อการแก้ไขปัญหาที่รวดเร็ว
การจัดเก็บประวัติการทำงาน สามารถใช้งานฟังก์ชันการเก็บประวัติเหตุการณ์ (Event History Collection Function) สำหรับการบันทึกประวัติ, เหตุการณ์, การทำงาน, ข้อผิดพลาด ฯลฯ ที่เกี่ยวข้องกับแต่ละหน่วยภายในไลน์การผลิต โดยจะถูกเก็บไว้ในหน่วย CPU ซึ่งสามารถตรวจสอบข้อมูลได้ใน GX Works 3
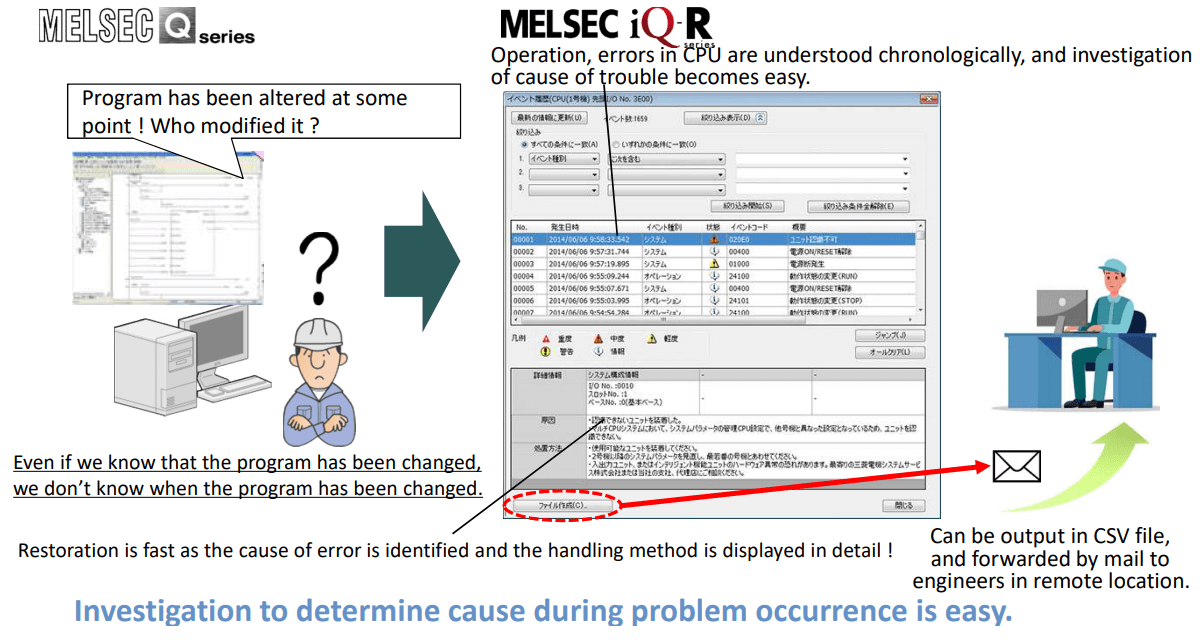
■ การบันทึกข้อมูลอุปกรณ์ก่อน-หลัง
ผ่านการใช้งานฟังก์ชันทริกเกอร์บันทึกข้อมูลของหน่วย CPU หรือหน่วยบันทึกข้อมูลความเร็วสูง (Trigger Logging Function of The CPU Unit or The High Speed Data Logger Unit) ทั้งก่อนและหลัง เพื่อให้สามารถระบุปัญหาที่เกิดขึ้น โดยการบันทึกและจัดเก็บไว้ใน SD การ์ด ซึ่งสามารถตั้งค่าการทำงานได้อย่างง่ายดายด้วยเครื่องมือเฉพาะ
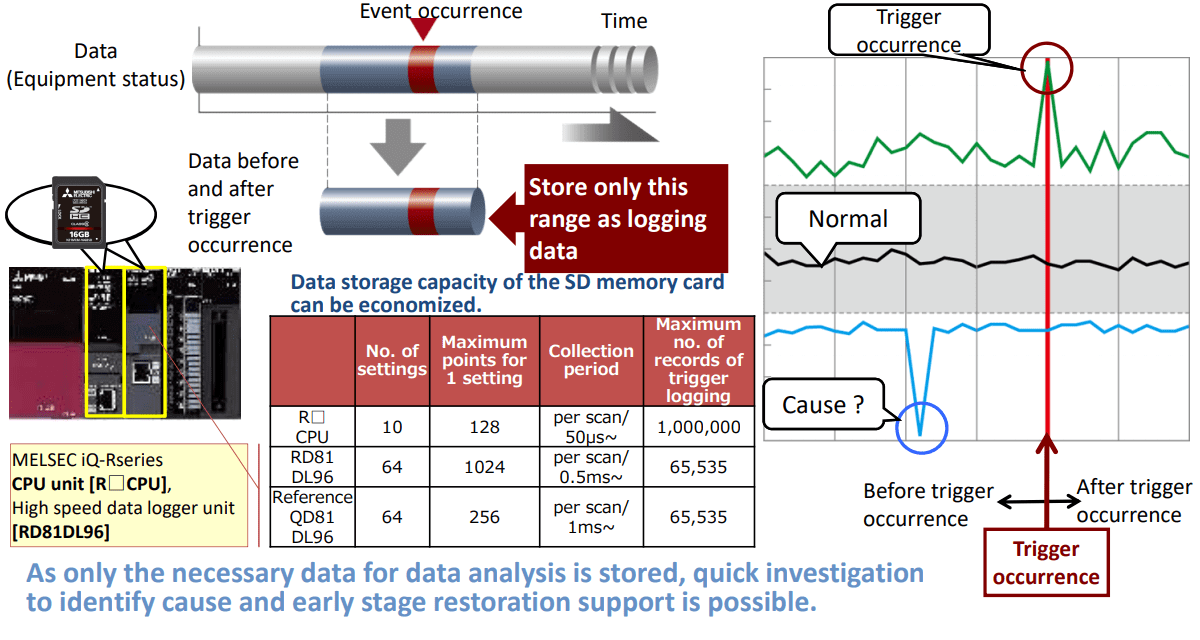
■ การยืนยันข้อผิดพลาดทางเทคนิค หรือ ความผิดพลาดของผู้ปฏิบัติงาน
ข้อผิดพลาดสามารถระบุ อุปกรณ์ / จุดผิดพลาด / เมื่อไหร่ / สาเหตุ สามารถตรวจสอบได้ผ่าน GOT โดยใช้ฟังก์ชันบันทึกการทำงาน (Operation Log Function) ของ GOT2000- สามารถบันทึกผู้ปฏิบัติงานในขณะนั้น
- สามารถบันทึกการรับรองความถูกต้องของผู้ปฏิบัติงาน หรือ การจัดการบันทึกการทำงาน
■ เพิ่มประสิทธิภาพอุปกรณ์และแก้ไขข้อผิดพลาดขณะเกิดปัญหา
ด้วยการใช้ฟังก์ชันการตรวจสอบแบบเรียลไทม์ (Real-time Monitoring Function) ของ GX LogViewer โดยสามารถตั้งค่าได้ง่าย ทำให้ผู้ใช้งานสามารถเข้าใจเวลาการเปลี่ยนแปลงในอุปกรณ์ ซึ่งตรวจสอบได้แบบ Real-time
■ การแสดงผลข้อมูลที่บันทึกเป็นกราฟ
ข้อมูลที่บันทึกสามารถแสดงผลเชื่อมโยงเป็นกราฟขั้นบันได ด้วยการตรวจสอบผ่าน ฟังก์ชันการตรวจสอบออฟไลน์ (Offline Monitor Function) โดยสามารถตรวจสอบการทำงานของอุปกรณ์ได้ตามลำดับเวลา จากการแสดงผลบนกราฟ
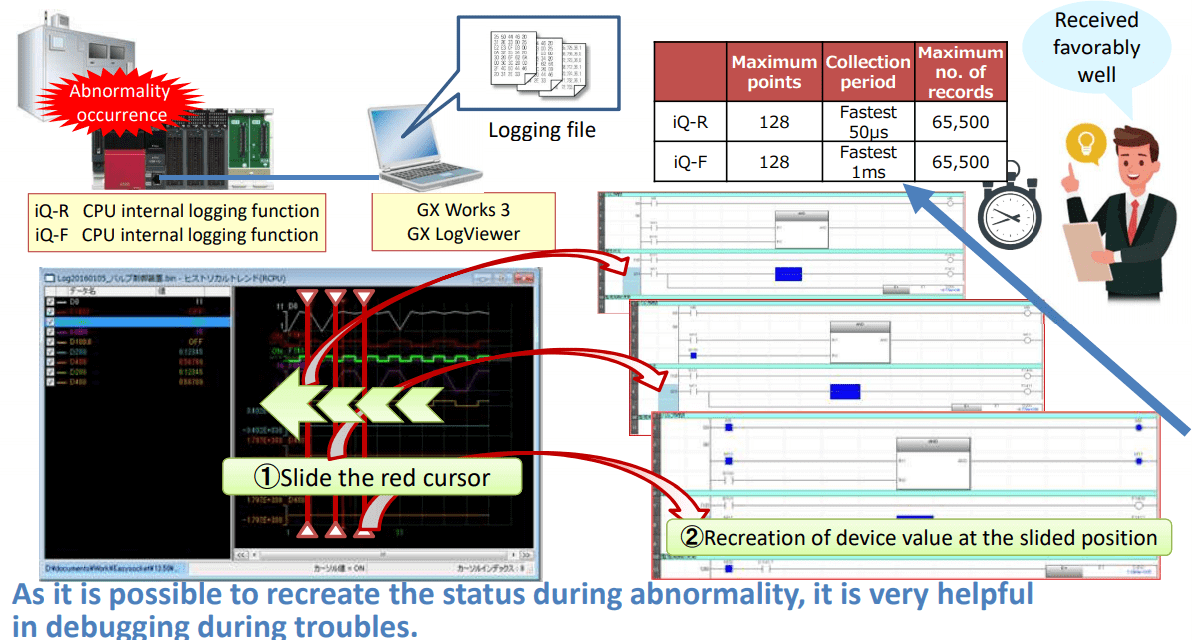
ใน GX LogViewer สามารถค้นหาข้อมูล หรือ เปรียบเทียบสถานะก่อน-หลังได้ นอกจากนี้ยังสามารถเชื่อมต่อกับโปรแกรมแลดเดอร์ที่เกี่ยวข้องเพื่อทำการตรวจสอบสถานะอุปกรณ์แบบออฟไลน์ได้ผ่าน GX Works 3 โดยข้อมูลทั้งหมดสามารถแสดงผลที่ทับซ้อนกันเป็นรูปคลื่นตามลำดับเวลาที่เกิดความผิดปกติ โดยสามารถซ้อนทับข้อมูลและตรวจสอบความแตกต่างของชุดข้อมูลแต่ละชุดได้อีกด้วย
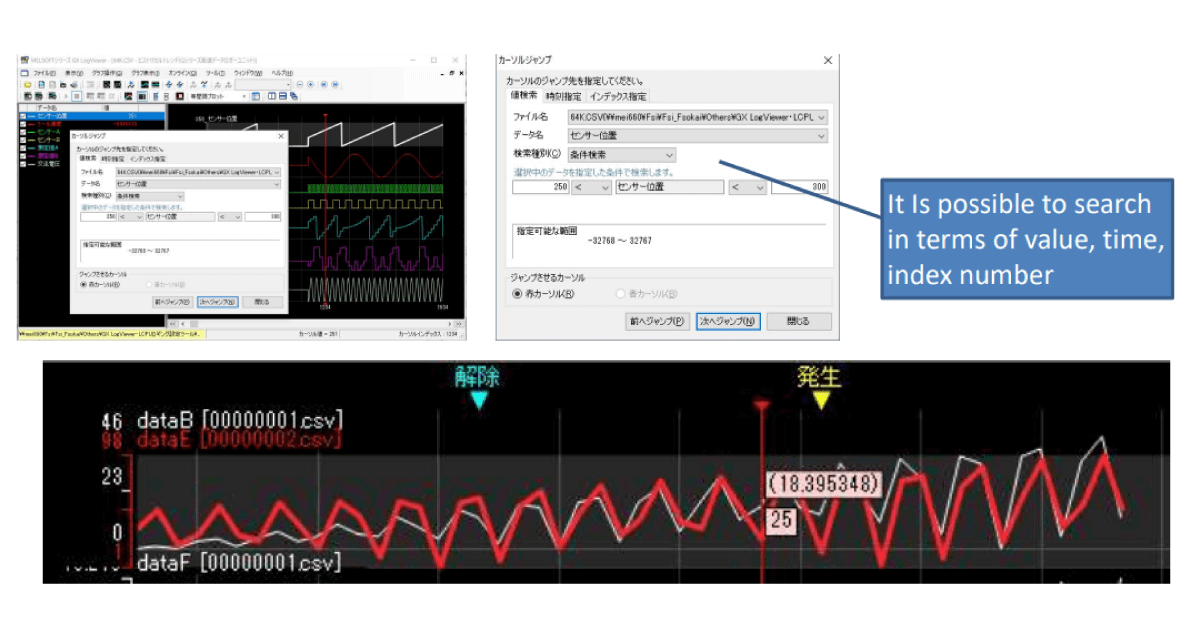
■ สร้างและจัดเก็บรายงานโดยอัตโนมัติ
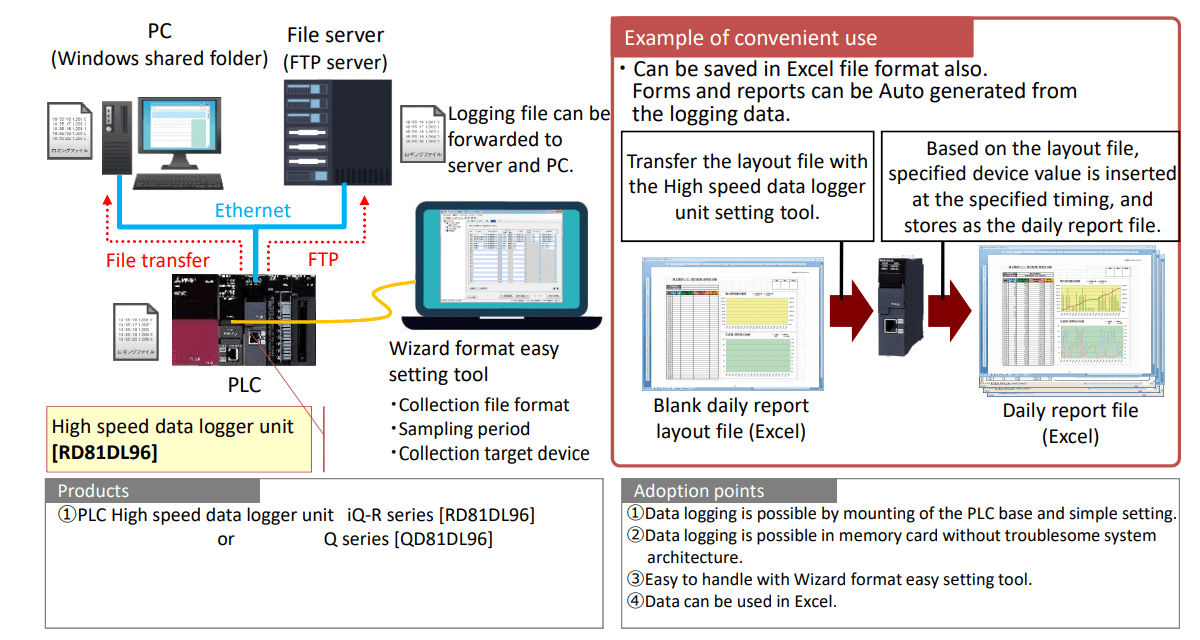
ด้วยการใช้งานเครื่องบันทึกข้อมูลความเร็วสูง (High Speed Data Logger Unit) โดยการส่งข้อมูลที่บันทึกไปยัง PC หรือ ไฟล์เซิร์ฟเวอร์ นอกจากนี้ยังสามารถใช้ ฟังก์ชันการสร้างรายงาน (Report Creation Function) สำหรับสร้างและจัดเก็บรายงานโดยอัตโนมัติ
■ การเก็บและใช้งานข้อมูลสถานที่ในฐานข้อมูล
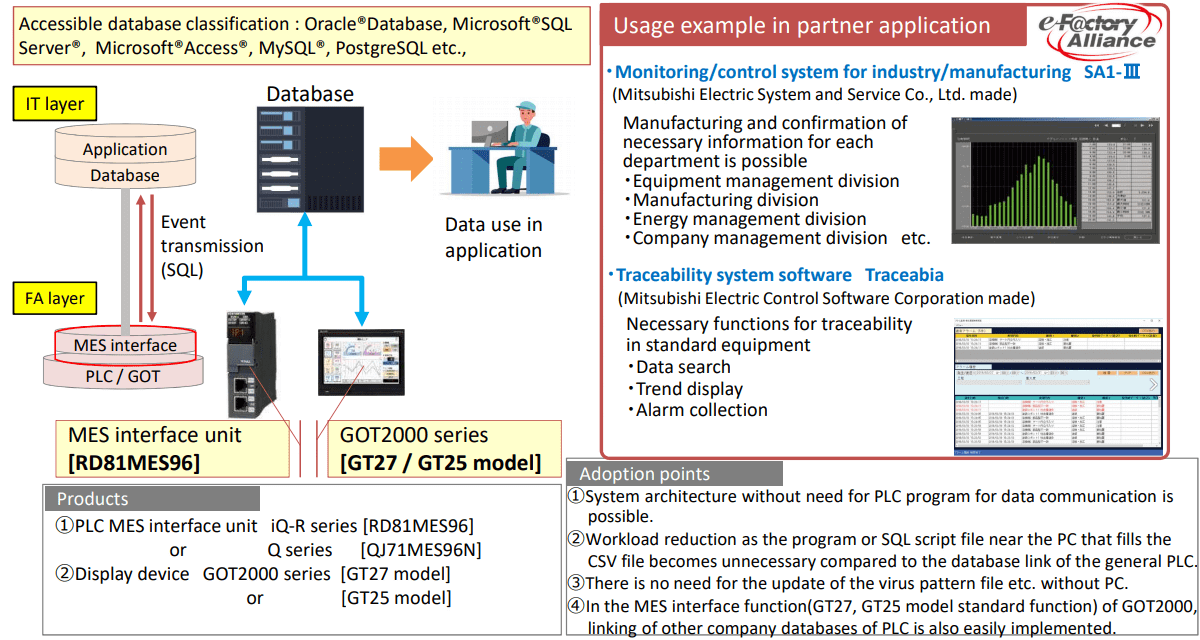
โดยใช้ยูนิตอินเตอร์เฟส MES (MES Interface Unit) หรือ ฟังก์ชัน GOT2000 MES (GOT2000 MES Function) เพื่อเชื่อมต่อกับฐานข้อมูลและ SQL โดยวิศวกรสามารถตั้งค่าด้วยเครื่องมือการตั้งค่าสำหรับสร้างรูปแบบที่ง่ายต่อการใช้งาน
■ ควบคุมการถ่ายโอนข้อมูลไปยัง PC แบบ Real-time
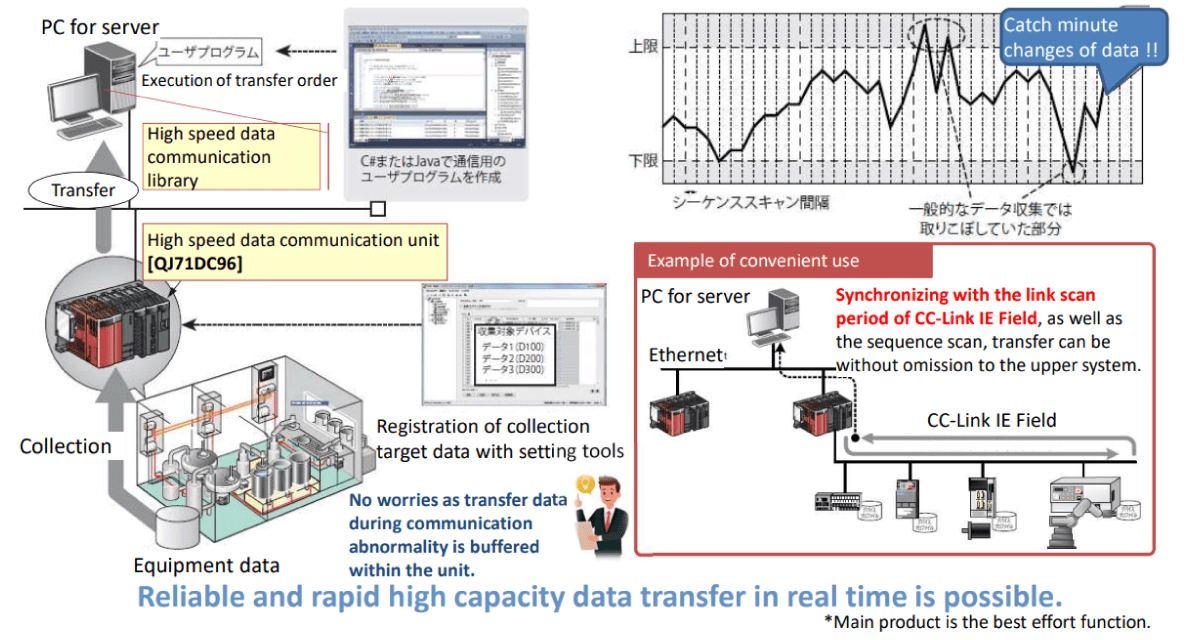
ด้วยการใช้ยูนิตการสื่อสารความเร็วสูง (High Speed Communication) สำหรับข้อมูลที่ซิงโครไนซ์กับลำดับการสแกนด้วยความแม่นยำสูง เพื่อให้สามารถถ่ายโอนข้อมูลแบบ Real-time ผ่านอีเธอร์เน็ตไปยัง PC
■ เชื่อมโยงวิดีโอระหว่าง GOT และเครือข่ายกล้องในไซต์
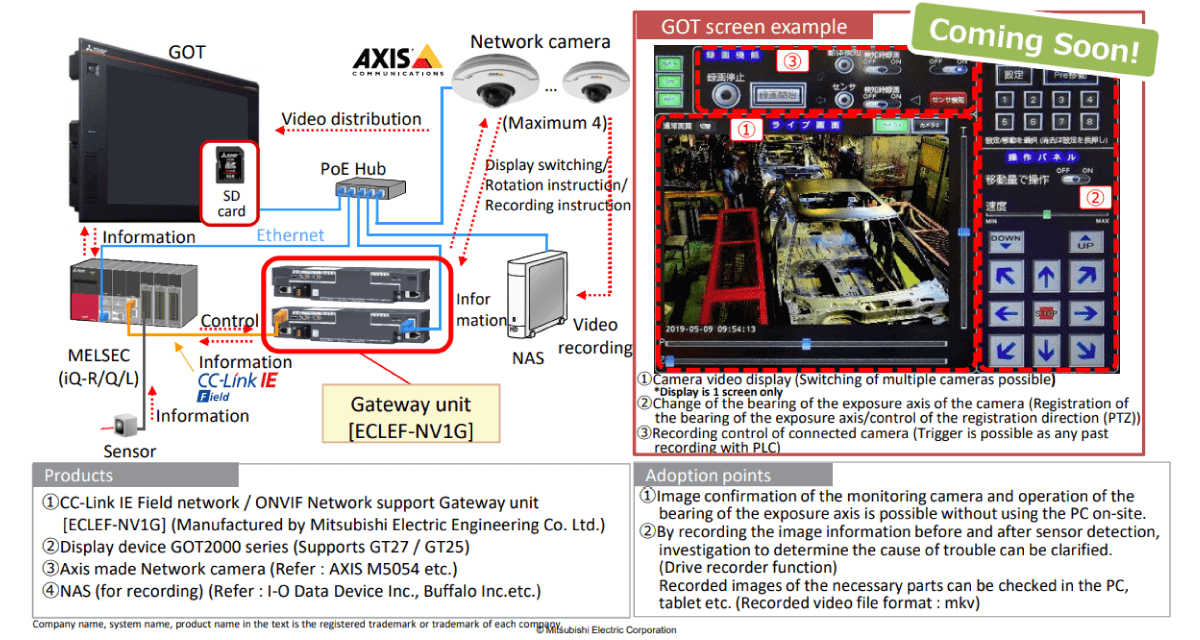
ด้วยการใช้ชุดเกตเวย์ ONVIF (ONVIF gateway) สำหรับการยืนยันภาพจากกล้องการทำงานของแบริ่ง, แกนแสงและฟังก์ชันไดรฟ์บันทึก ซึ่งสามารถใช้งานได้ผ่าน GOT
■ ข้อมูลบันทึกเชื่อมโยงของวิดีโอและข้อมูลการควบคุม
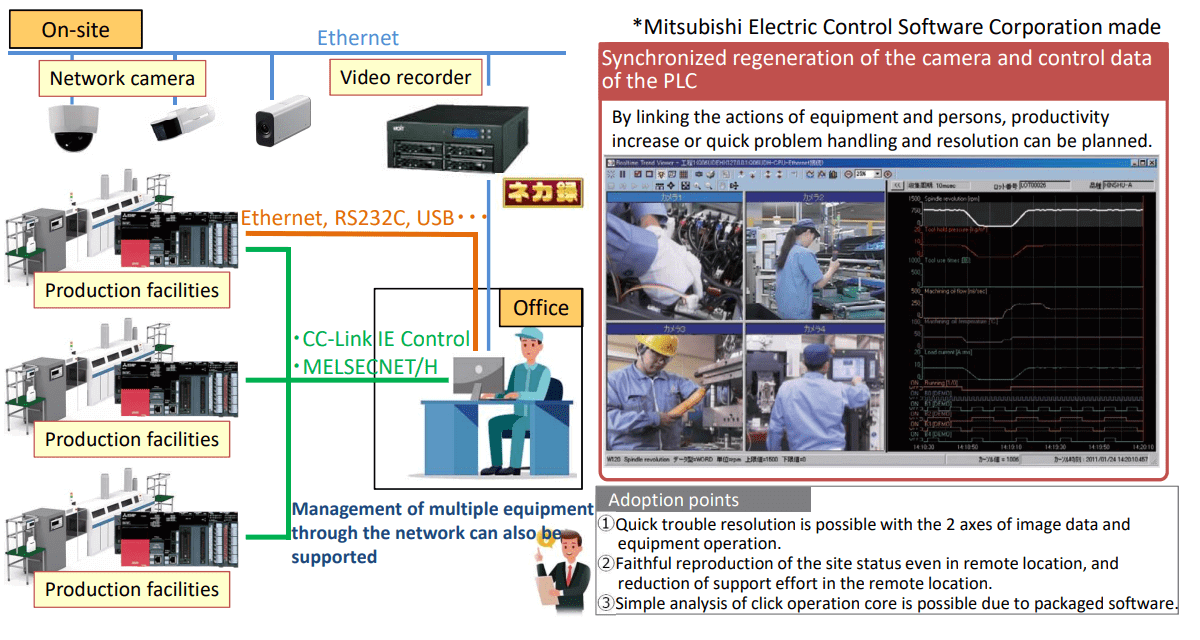
ด้วยการใช้ซอฟต์แวร์การรวบรวมข้อมูล (Data collection software) [Miranda-VR] (ผลิตโดย Mitsubishi Electric Control Software) สำหรับการเชื่อมโยงข้อมูลวิดีโอและการควบคุม เพื่อระบุสาเหตุของปัญหาและการตรวจสอบสถานะที่สามารถทำได้อย่างรวดเร็ว
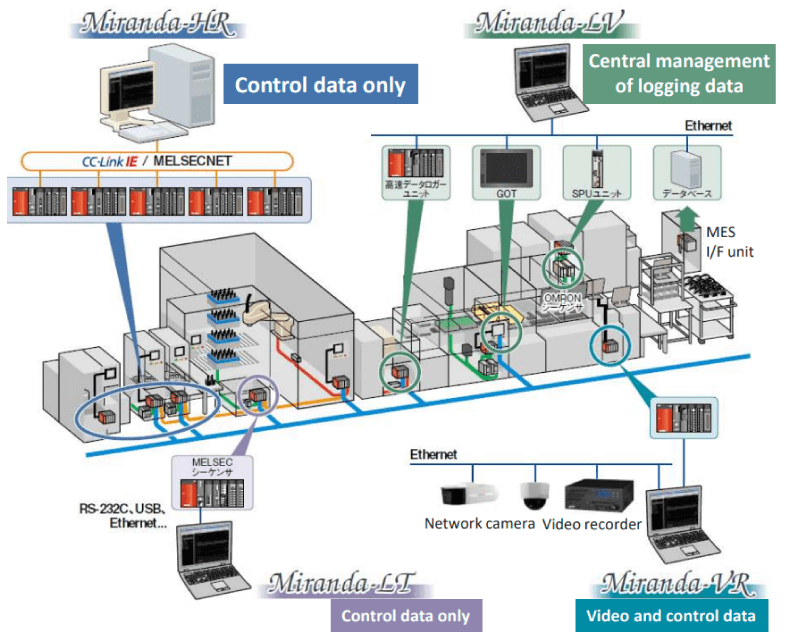
ข้อแนะนำการใช้งานซอฟต์แวร์การรวบรวมข้อมูล (Data collection software) [Miranda-VR] 1. สามารถกำหนดค่าการติดตั้งแบบกำหนดได้เอง ผ่านเครื่องมือทางวิศวกรรมอย่างง่าย
2. ข้อมูลวิดีโอและการควบคุมสามารถเก็บไว้ใน HD ความจุสูง (สามารถทำซ้ำได้)
3. รองรับการใช้ร่วมกับกล้องเครือข่าย ONVIF
4. สามารถขยายระยะห่างของกล้องได้สูงถึง 100m (สามารถต่อขยายได้ด้วย HUB)
5. สามารถบันทึกหน้าจอ PC หรือ GOT เป็นไฟล์ภาพ
■ การตั้งค่า /ปรับแต่ง /ตรวจสอบ Servo โดยไม่ใช้ PC
ด้วยการใช้ GOT Drive ส่วนหนึ่งของฟังก์ชัน (การตั้งค่า / ปรับแต่ง / ตรวจสอบ) ที่มีใน MR Configurator2 (รองรับกับ Servo MR-J4) โดยสามารถนำไปใช้ใน GOT ได้
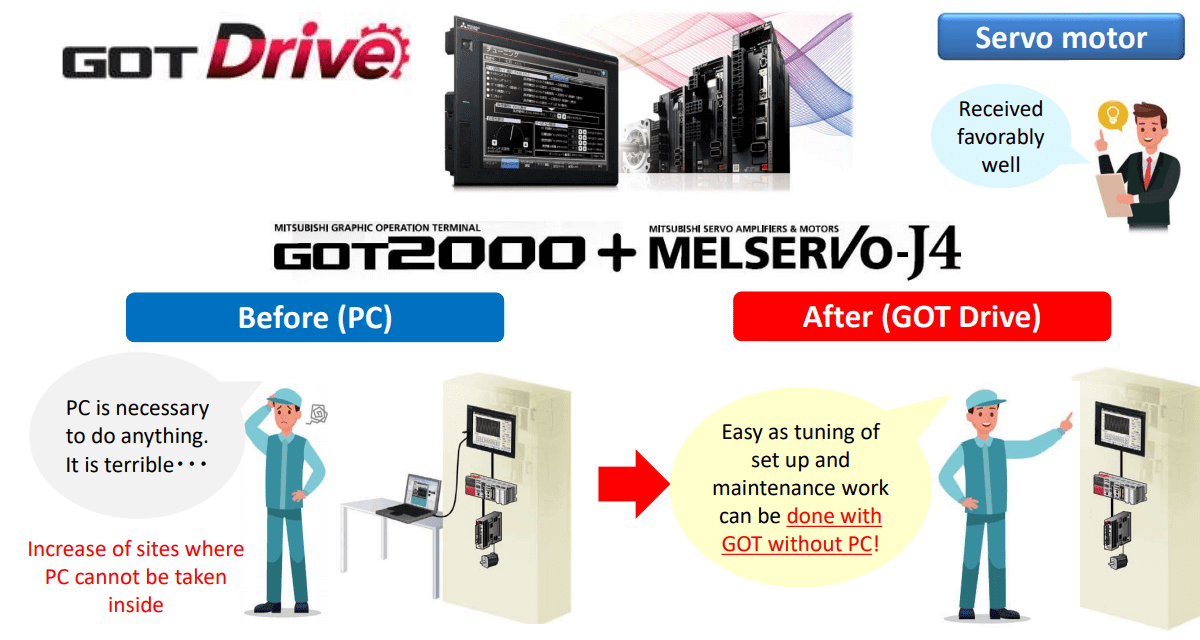
■ การปรับแต่ง Servo ในทันทีโดยไม่ต้องใช้ PC
การปรับแต่งในสัมผัสเดียว ด้วยการตั้งค่าจากปุ่มบนหน้าจอ GOT2000 โดยไม่ต้องเชื่อมต่อ PC ทำให้ลดอุปสรรคในการทำงานที่ต้องเชื่อมต่อกับ PC ซึ่งสามารถปรับแต่งค่าการใช้งานผ่าน MR Configurator 2 ได้
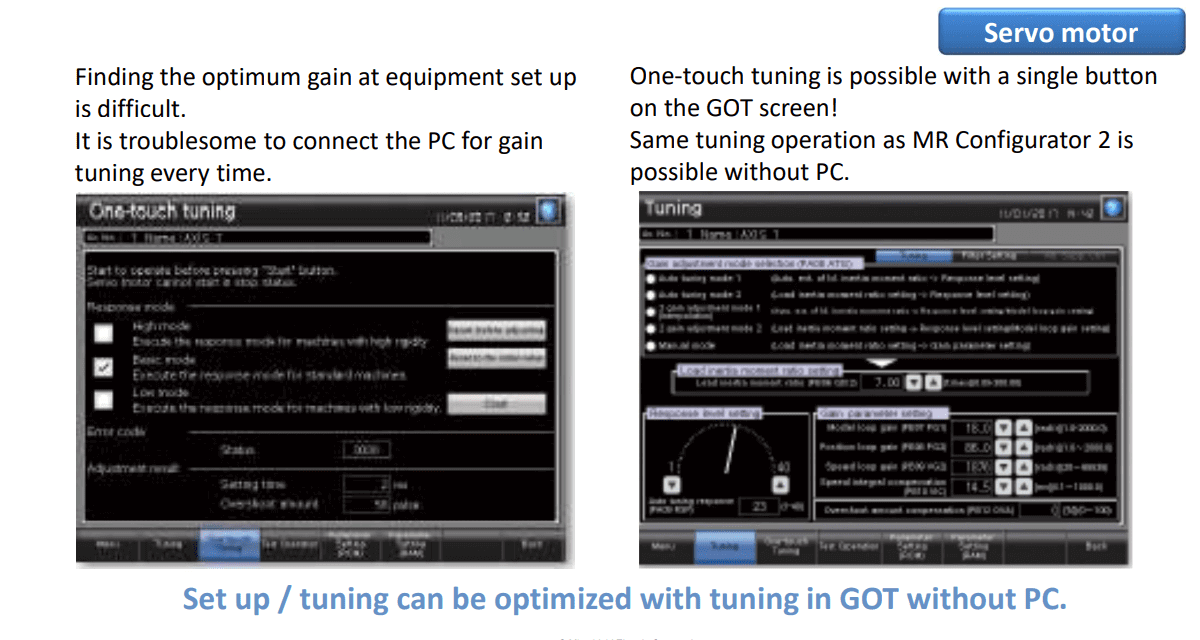
■ การแสดงค่าข้อมูลกราฟรูปคลื่น โดยไม่ต้องใช้ PC
ข้อมูลของ Servo (กระแสไฟฟ้า, มอเตอร์, ตำแหน่ง ฯลฯ ) ทั้งก่อนและหลังสามารถอ่านและแสดงผลเป็นกราฟรูปคลื่นหรือรายการข้อมูล ด้วยฟังก์ชันบันทึก (Drive Recorder Function) ของ GOT2000
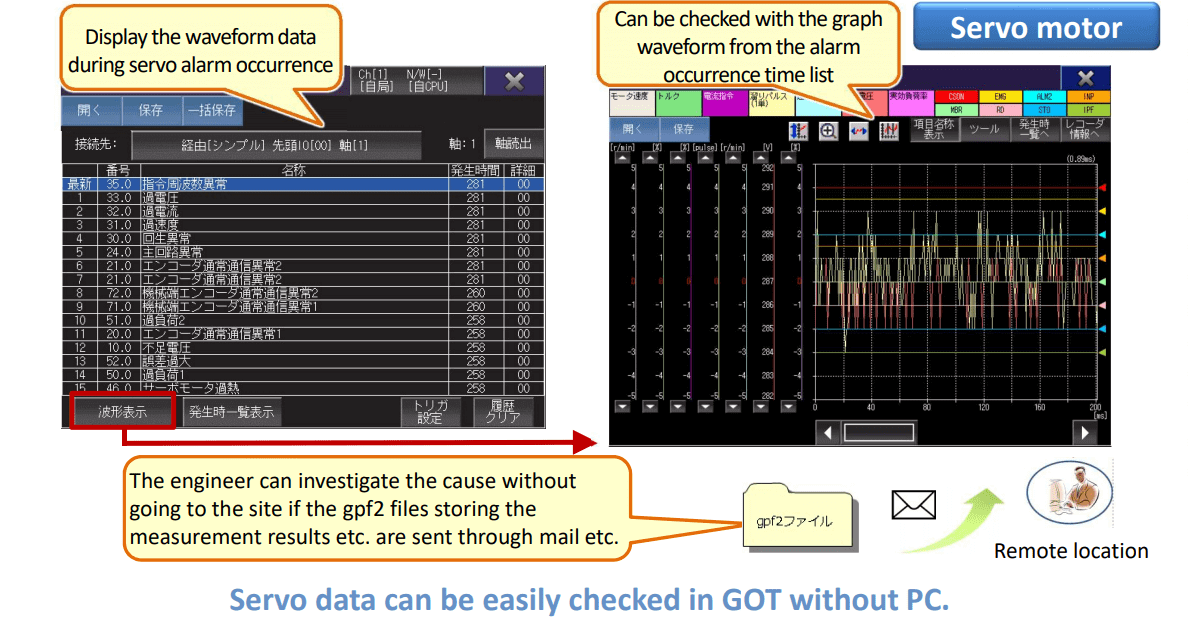
■ การบำรุงรักษา Inverter โดยไม่ต้องเปิดแผงควบคุม
การตั้งค่าความถี่เอาต์พุตของ Inverter, แรงดันไฟฟ้า ฯลฯ สามารถตรวจสอบได้ผ่าน GOT ด้วยฟังก์ชันการตรวจสอบแบตช์ (batch monitoring function) ของ GOT2000 โดยการตั้งค่าพารามิเตอร์ของ Inverter สามารถปรับได้ใน GOT ด้วยฟังก์ชันการตั้งค่าพารามิเตอร์ (Parameter Setting (Simple mode))
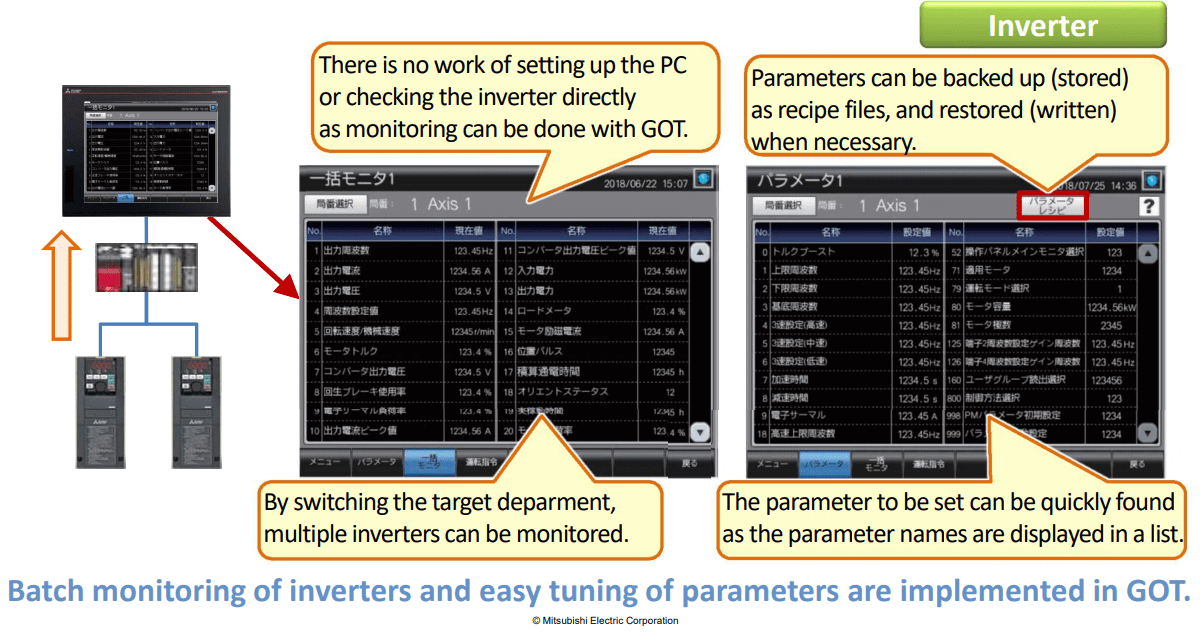
■ การติดตั้ง หรือ ปรับแต่ง Robot อย่างง่าย
การตั้งค่าการทำงานของหุ่นยนต์สามารถทำได้ผ่าน ฟังก์ชันเชื่อมโยงกับหุ่นยนต์ (Robot Linking Function) ของ GOT2000 ทำให้สามารถควบคุมการทำงานของ jog และการทำงานของมือหุ่นยนต์ เป็นต้น โดยสามารถทำได้จากหน้าจอ GOT
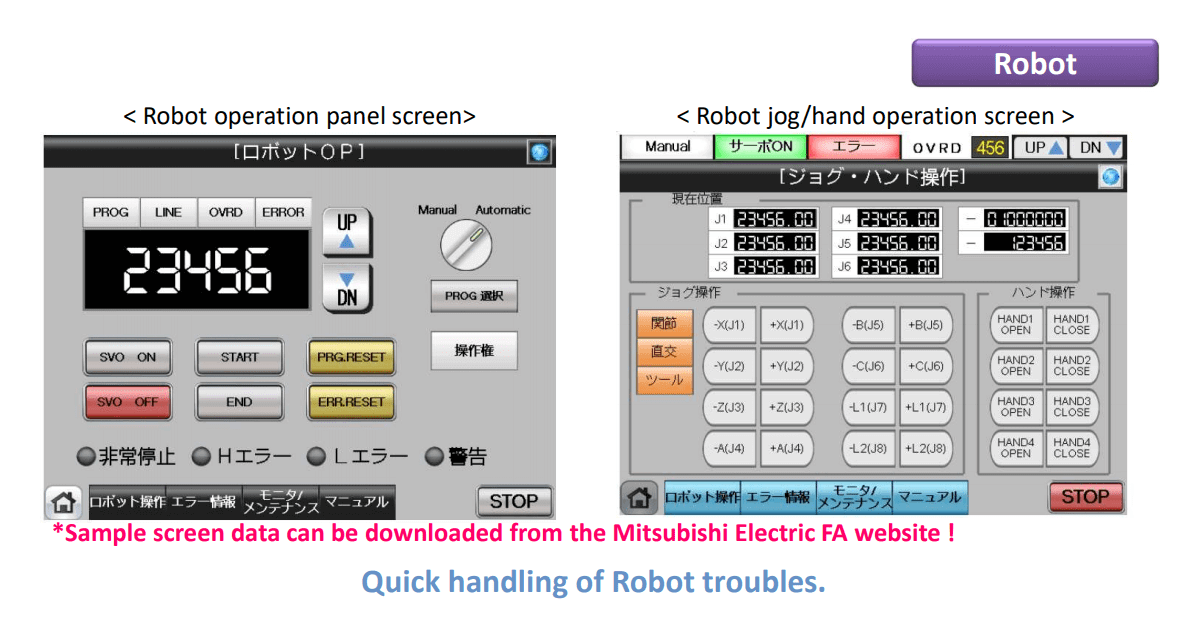
3. ฟังก์ชันการป้องกันปัญหาที่อาจเกิดขึ้น
■ การป้องกันความผิดพลาดของระบบโดยการตรวจสอบอายุการใช้งานรีเลย์ (Relay)
ด้วยการนับจำนวนครั้งที่รีเลย์ (Relay) เปิดอยู่ในยูนิตเอาต์พุต โดยจะมีการแจ้งเตือนรีเลย์ (Relay) ใกล้หมดอายุการใช้งาน ทำให้สามารถแก้ไขการหยุดการทำงานได้ทันท่วงที พร้อมกับระบบป้องกันหน่วยเอาต์พุตทั้งระบบป้องกันความร้อนและระบบป้องกันกระแสไฟฟ้าเกิน
■ ลดค่าใช้จ่ายการบำรุงรักษาและลดเวลาการติดตั้งขั้วสปริง
ด้วยการใช้ผลิตภัณฑ์บล็อกเทอร์มินัลสปริง (Spring Clamp Terminal Block) iQ-R หรือ iQ-F ทำให้สามารถป้องกันสาเหตุของสายไฟฟ้าคลาย เนื่องจากการสั่นได้
■ ป้องกันการเข้าถึงเครือข่ายที่ไม่ได้รับอนุญาต
ด้วยการลงทะเบียน IP ที่สามารถเข้าถึงหน่วย CPU ทำให้สามารถตรวจสอบการเข้าถึงหน่วย CPU อื่นนอกเหนือจากที่ได้รับอนุญาต รวมถึงสามารถจัดการตั้งค่าระบุ User และ Password ให้การเข้าสู่ระบบของผู้ปฏิบัติงาน เพื่อรับรองความถูกต้องผ่าน GOT2000 ได้
■ ตรวจสอบอายุการใช้งานของเครื่องจักร
ตรวจสอบข้อมูลเครื่องจักรได้ผ่าน Servo โดยไม่ต้องเชื่อมต่อกับ PC ใน GOT2000 ผ่านฟังก์ชันการวินิจฉัยเครื่องจักร (Machine diagnostic function) และสามารถตรวจสอบอายุการใช้งานของคอนเดนเซอร์ (Condenser) และรีเลย์ (Relay) ของ Servo Amplifier ได้ผ่านฟังก์ชันการวินิจฉัยอายุการใช้งานของ Servo (Amplifier lifetime diagnostic function)
■ ตรวจสอบการทำงานและบำรุงรักษาเชิงป้องกันของอุปกรณ์
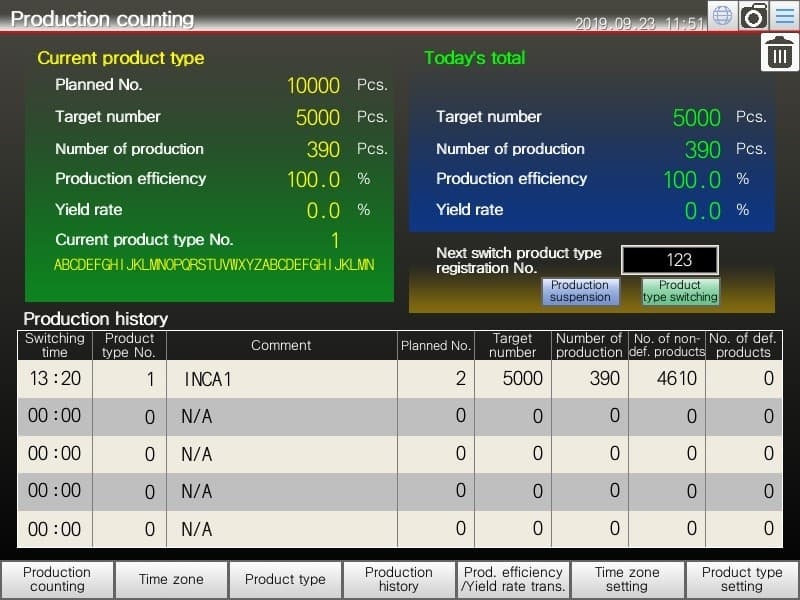
แสดงข้อมูลการผลิต เช่น จำนวนผลิตภัณฑ์ทั้งหมด หรือจำนวนผลิตภัณฑ์ที่ผ่าน QC นอกจากนี้ยังสามารถแสดงผลได้ทั้งข้อมูลในอดีตและปัจจุบันด้วยการกำหนดประเภทผลิตภัณฑ์ (Product Type) และ Time Zone
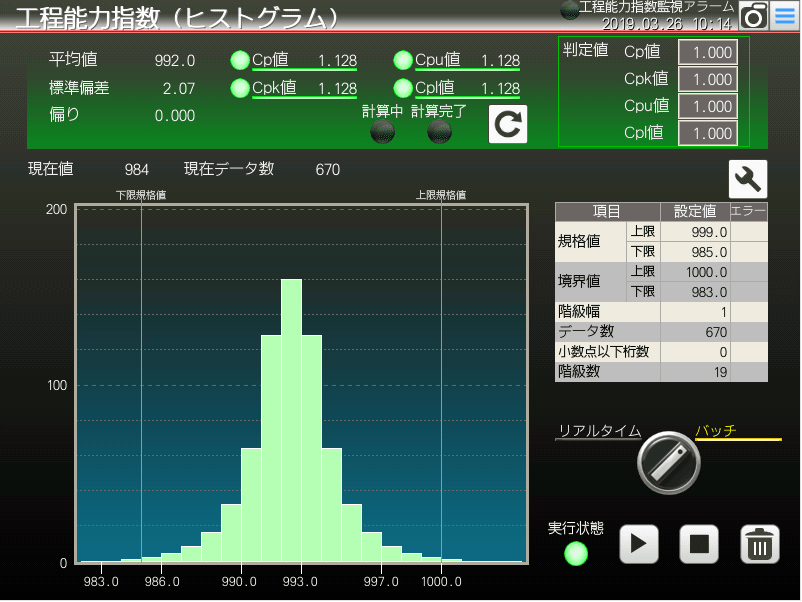
สามารถตรวจสอบเสถียรภาพของกระบวนการผลิตได้ในแบบ real-time ด้วยการแสดงสถานะของเครื่องจักร จึงทำให้สามารถปรับปรุงกระบวนการได้ทันทีด้วยการตรวจสอบค่าการกระจายและตรวจสอบสัญญาณการแจ้งเตือนของดัชนีชี้วัดความสามารถกระบวนการ *1 ดัชนีชี้วัดความสามารถกระบวนการ คือดัชนีที่ประเมินความสามารถในการผลิตในเชิงปริมาณภายในข้อมูลจำเพาะ
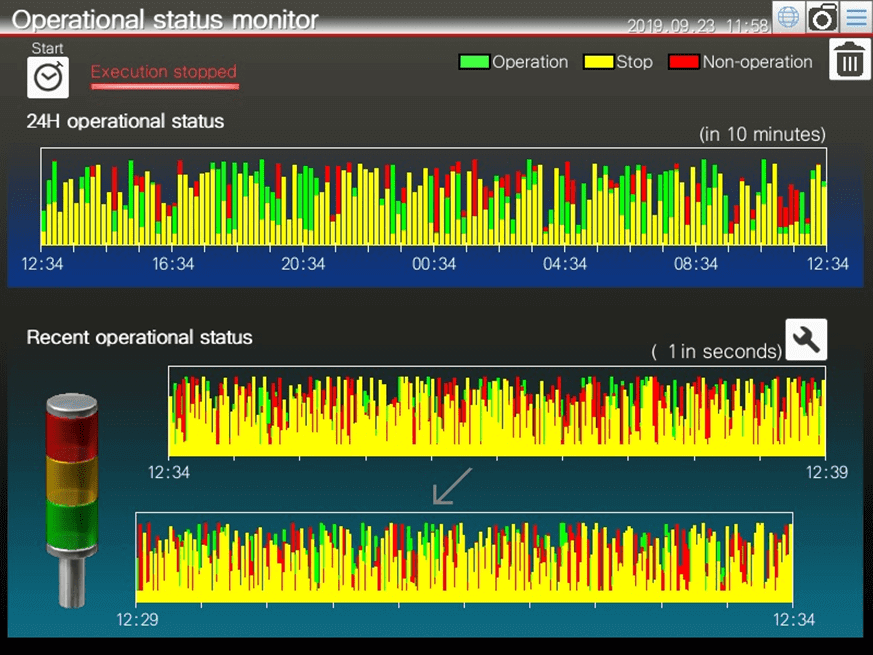
แสดงสถานะการทำงานของเครื่องจักร เช่น operating/ stopped/ non-operating ในรูปแบบของกราฟเวลา และแสดงสถานะของเครื่องจักรแบบ real-time
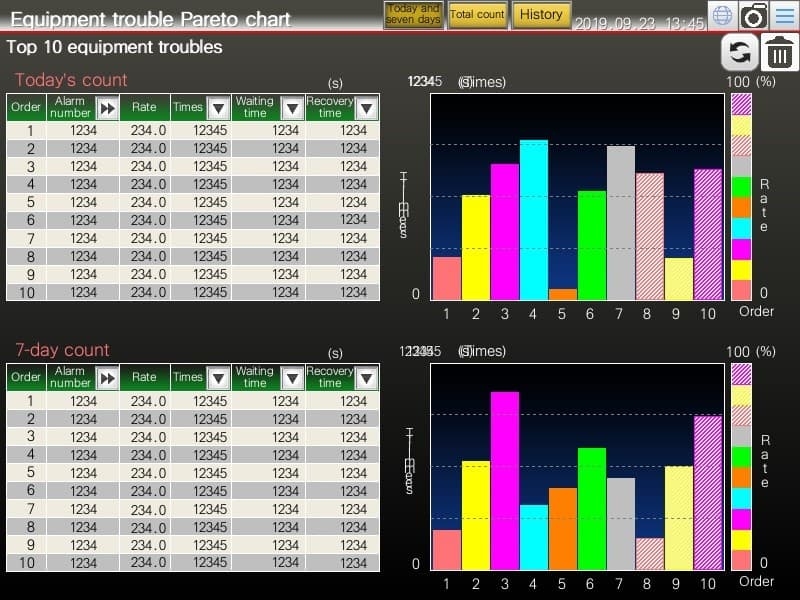
ฟังก์ชันนี้จะแสดงการเกิดความผิดปกติของเครื่องจักร ทำให้สามารถทราบถึงต้นเหตุที่ทำให้ประสิทธิภาพการผลิตลดลงได้อย่างง่ายดายด้วยการรวบรวมข้อมูลการแจ้งเตือนที่เกิดขึ้นทั้งหมดและแสดงในแผนภูมิพาเรโต
(Xbar-R chart)
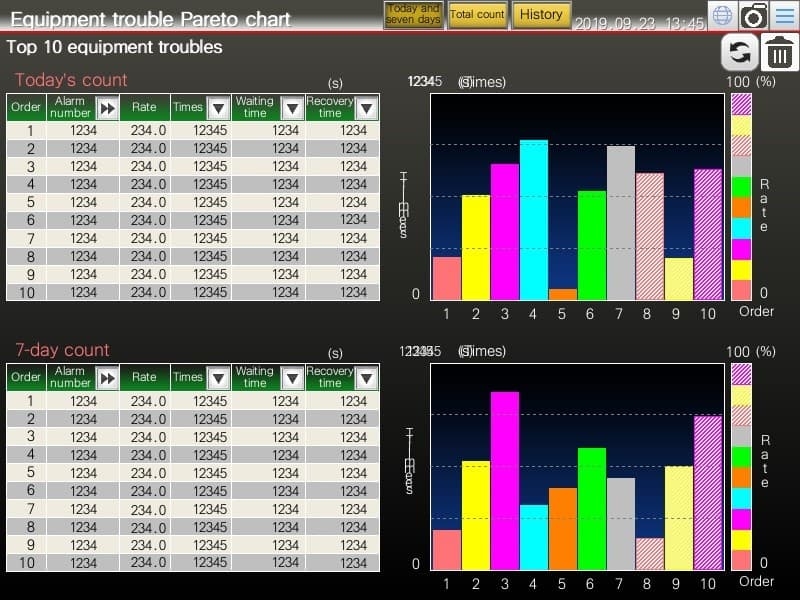
สามารถตรวจสอบเสถียรภาพของกระบวนการผลิตได้ในแบบ real-time จึงสามารถทำการปรับปรุงได้ทันทีด้วยการตรวจสอบสัญญาณเตือนและเช็คการผันแปรของคุณภาพด้วยแผนภูมิการควบคุม Xbar-R chart
(Loss time analysis)
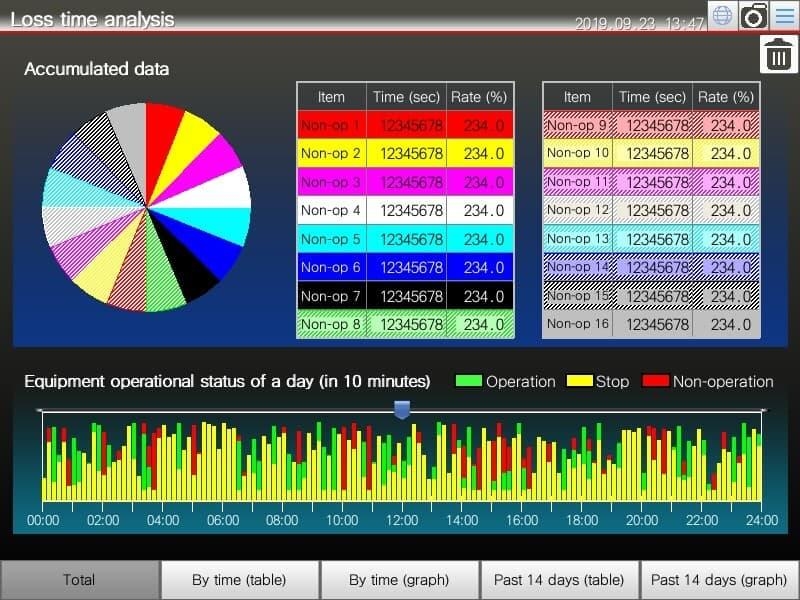
ฟังก์ชันนี้สามารถวิเคราะห์ได้มากถึง 16 Major Losses และ 7 Wastes ที่ทำให้ประสิทธิภาพการผลิตลดลง โดยการตรวจวัดอัตราการเกิด Downtime ของแต่ละปัจจัย และแสดงผลได้ใน 3 รูปแบบ เปอร์เซ็นต์สะสม, Time zone และค่า 14 วันย้อนหลัง
ทั้งหมดนี้เป็นเพียงส่วนหนึ่งของโซลูชันลดการหยุดทำงานของเครื่องจักร ‘Downtime reduction’ ที่ Mitsubishi Electric ได้นำเสนอเพื่อให้ตอบโจทย์การทำงานของอุตสาหกรรม ซึ่งการแก้ไขปัญหานั้นจะสามารถช่วยให้ระบบการทำงานเป็นไปอย่างราบรื่น ไม่มีสะดุด และช่วยลดต้นทุนในการบำรุงรักษา รวมถึงทำให้ผลผลิตของอุตสาหกรรมมีประสิทธิภาพ และรวดเร็วตามระยะเวลาที่กำหนดไว้อีกด้วย