5 ตัวอย่าง กรณีการใช้ System Recorder ในอุปกรณ์ MELSEC iQ-R
PLC เป็นอุปกรณ์การประมวลผลที่สำคัญภายระบบอุตสาหกรรมการผลิต ที่ช่วยให้การผลิตสามารถสั่งการและทำงานได้แบบอัตโนมัติง่ายดายมากยิ่งขึ้น โดยภายใน PLC ซีรีส์ MELSEC iQ-R ก็ประกอบด้วยฟังก์ชันการทำงานหลากหลายรูปแบบ แต่ในวันนี้ Mitsubishi Electric ขอนำเสนอ “ฟังก์ชันการบันทึกสถานะการทำงานของระบบและการวิเคราะห์อย่างง่าย”
เครื่องบันทึกระบบเป็นโซลูชันการบำรุงรักษาแบบแยกส่วน สำหรับการลด Downtime ในพื้นที่การผลิตอย่างมีประสิทธิภาพ ด้วย การบันทึกสถานะการทำงานของทั้งระบบ (System Recorder) โดยเมื่อเกิดข้อผิดพลาดขึ้นจะช่วยให้อุตสาหกรรมสามารถเปิดการทำงานการวิเคราะห์อย่างง่าย เพื่อตรวจสอบระบบนั่นเอง
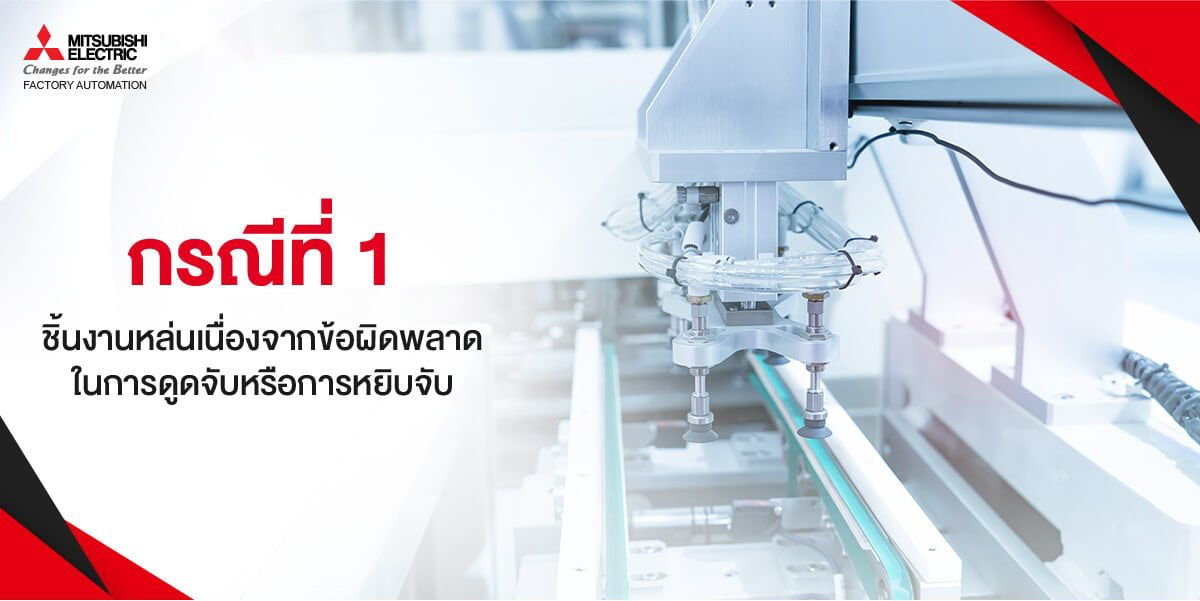
กรณีที่ 1 ชิ้นงานหล่นเนื่องจากข้อผิดพลาดในการดูดจับหรือการหยิบจับ
ปัญหาที่เกิดขึ้นในพื้นที่การผลิต
1. เกิดข้อผิดพลาดในอุปกรณ์ขั้นตอนการขนส่งชิ้นงานโดยใช้กลไกการดูด
2. แม้ว่าจะมีการตรวจสอบอุปกรณ์ แต่ชิ้นงานไม่ได้ติดตั้งในตำแหน่งที่ระบุ ทำให้ไม่มีการแสดงข้อผิดพลาด
3. ไม่สามารถทราบถึงสภาพการใช้งานของอุปกรณ์เมื่อเกิดข้อผิดพลาด เนื่องจากไม่มีตัวดำเนินการอยู่รอบ ๆ อุปกรณ์ หรือไม่สามารถระบุสาเหตุของข้อผิดพลาดของอุปกรณ์ได้นั่นเอง
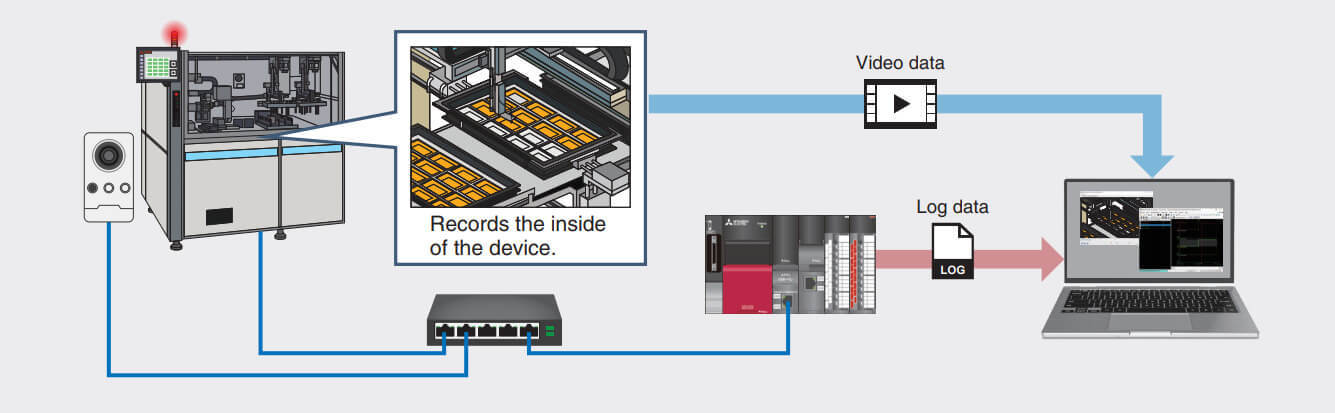
โซลูชันการจัดการปัญหาการดูดจับด้วยระบบบันทึก (System Recorder)
1. การตรวจสอบวิดีโอที่บันทึกไว้ก่อนที่ปัญหาจะเกิดขึ้น (GX Video Viewer) แสดงให้เห็นช่วงเวลาที่ชิ้นงานหลุดจากอุปกรณ์ดูดจับ ซึ่งสามารถทำเครื่องหมายบนตำแหน่งที่ตรงกันบนแถบค้นหา ด้วยฟังก์ชันเครื่องหมายบันทึก (Log Marker Function)
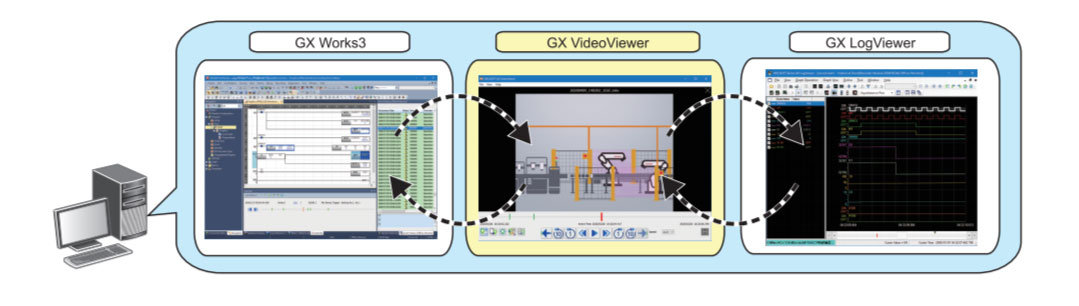
2. การตรวจสอบข้อมูลในช่วงเวลาที่กำหนด โดยซอฟต์แวร์ GX LogViewer ใน MELSEC iQ-R สามารถแสดงค่าความดันสูญญากาศที่ลดลง ก่อนที่ระบบจะเปิดคำสั่ง "ปิดการดูดจับ (suction OFF)"
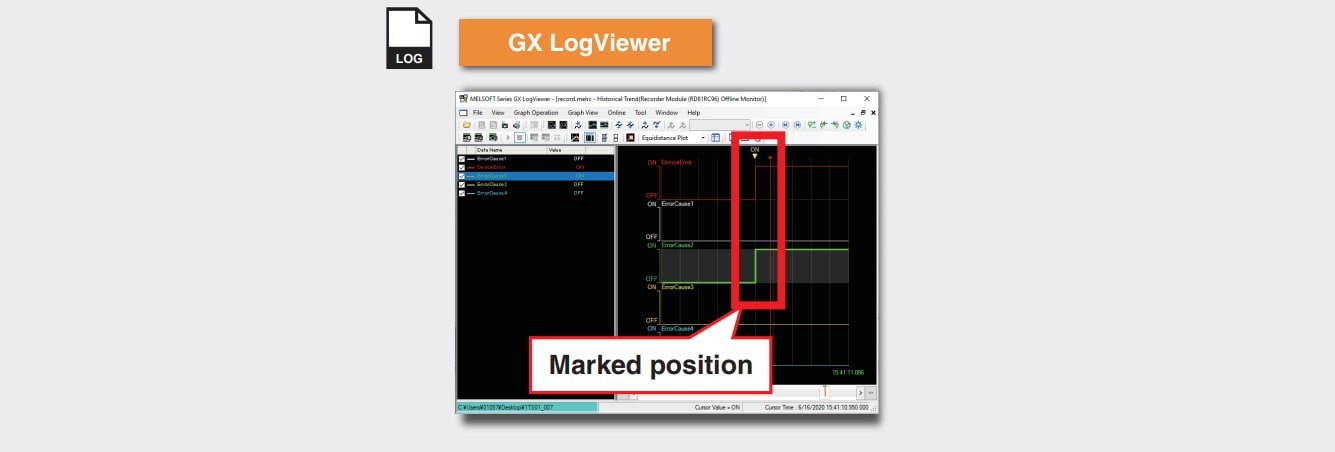
ในกรณีเกิดข้อผิดพลาดที่ชิ้นส่วนดูดจับ แต่ก็ไม่สามารถระบุสาเหตุได้ เนื่องจากชิ้นงานที่ตกหล่นถูกติดตั้งในตำแหน่งที่ไม่ถูกต้อง ซึ่งระบบบันทึก (System Recorder) สามารถระบุได้ว่าสาเหตุเกิดจากแรงดันสูญญากาศในส่วนดูด
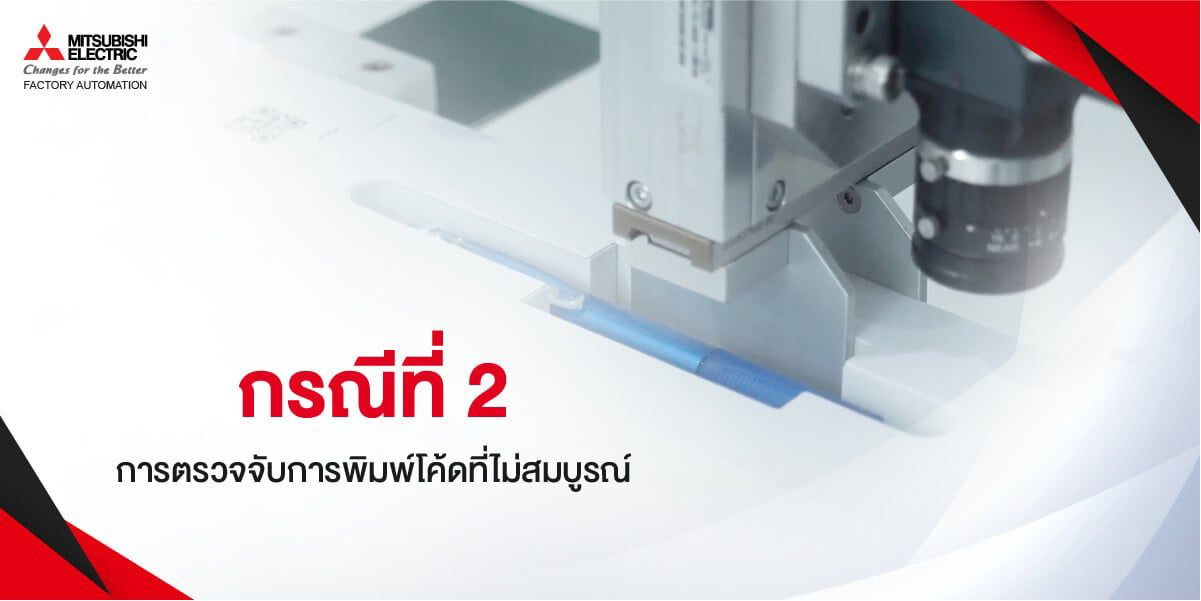
กรณีที่ 2 การตรวจจับการพิมพ์โค้ดที่ไม่สมบูรณ์
ปัญหาที่เกิดขึ้นในพื้นที่การผลิต
1. การพิมพ์ QR Code ด้วยเครื่องพิมพ์เลเซอร์
2. ตรวจพบข้อผิดพลาดการพิมพ์ QR Code ในขั้นตอนสุดท้าย
3. สาเหตุที่เป็นไปได้ เช่น ชิ้นงานไม่ตรงจากตำแหน่งที่กำหนด เกิดความล้มเหลวในการควบคุมในเลเซอร์กำหนดตำแหน่ง ทำให้ไม่สามารถระบุสาเหตุของความล้มเหลวในการพิมพ์ได้
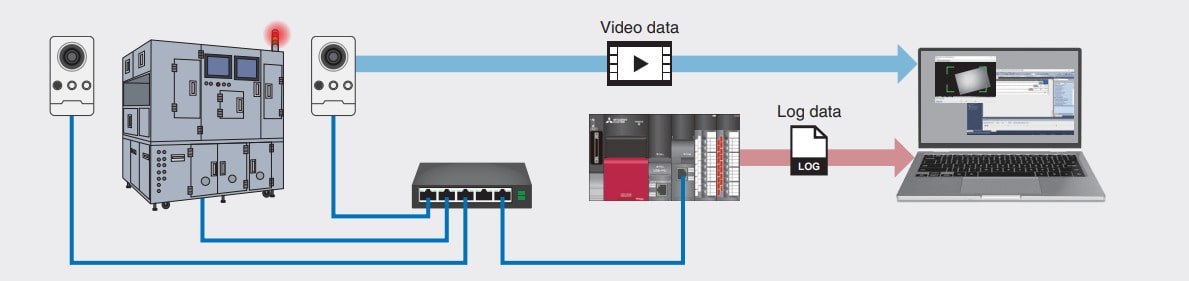
โซลูชันการจัดการปัญหาการพิมพ์โค้ดด้วยระบบบันทึก (System Recorder)
1. การตรวจสอบชิ้นงานที่เกิดความล้มเหลวในการพิมพ์ โดยการตรวจสอบชิ้นงานที่อยู่ไม่ตรงกับแนวตำแหน่งที่ระบุ จากวิดีโอที่บันทึกไว้ (Video Verification Tool)
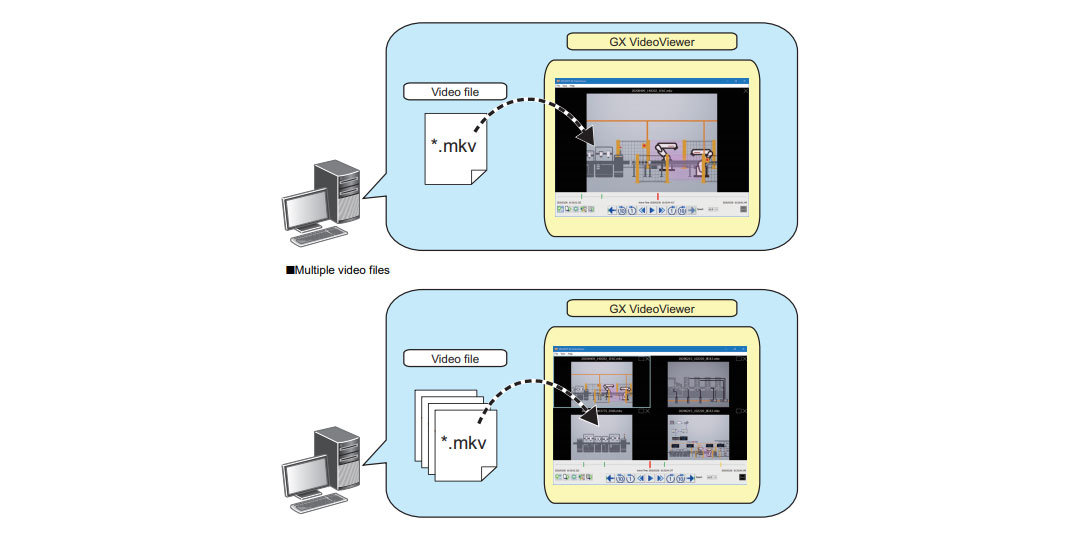
2. ฟังก์ชันการตรวจสอบแบบออฟไลน์ (The Offline Monitoring Function) ภายใน GX Works3 สำหรับตรวจสอบปัญหาสวิตช์อัตโนมัติของกระบอกจับอากาศภายในขั้นตอนการขนส่งสามารถทำงานได้ตามปกติหรือไม่
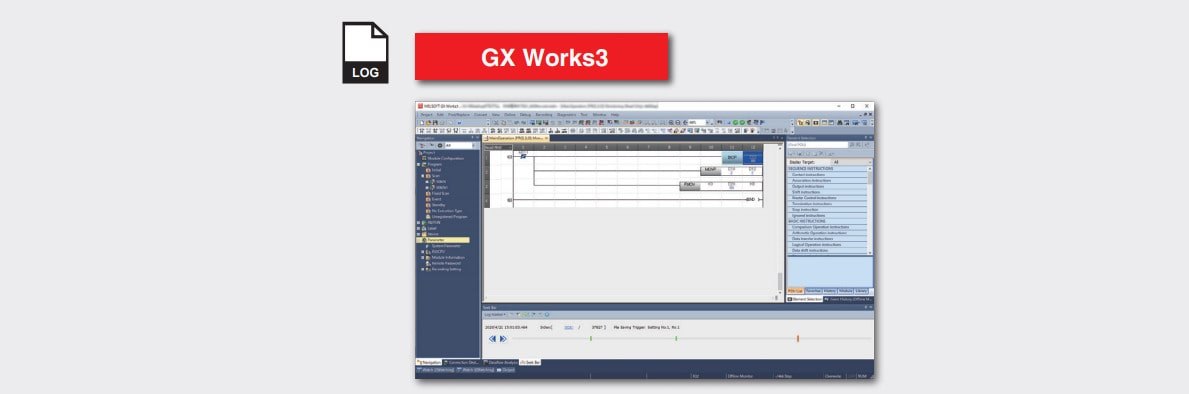
3. การตรวจสอบผ่านภาพวิดีโอ เพื่อตรวจสอบหัวจับที่สัมผัสกับชิ้นงาน ซึ่งอาจทำให้เกิดปัญหาชิ้นงานอยู่ในแนวที่ไม่ตรงจากตำแหน่งที่ระบุอย่างมีนัยสำคัญ โดยระบบบันทึก (System Recorder) สามารถระบุสาเหตุมาจากการที่ชิ้นงานไม่ตรงแนวตำแหน่ง
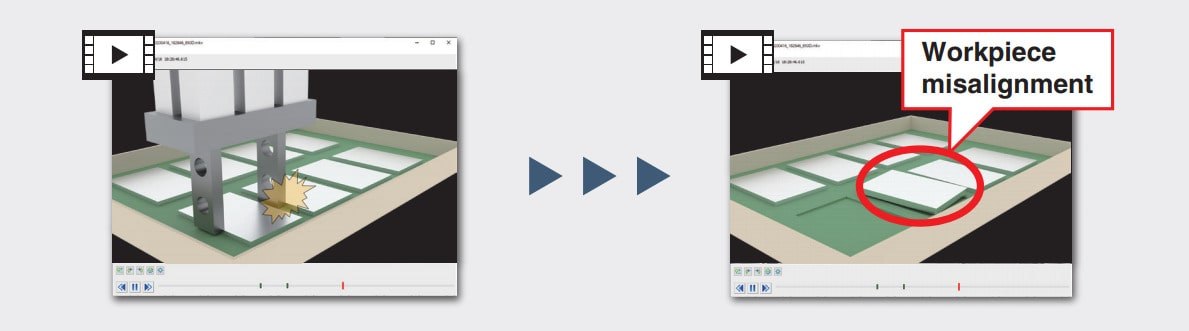
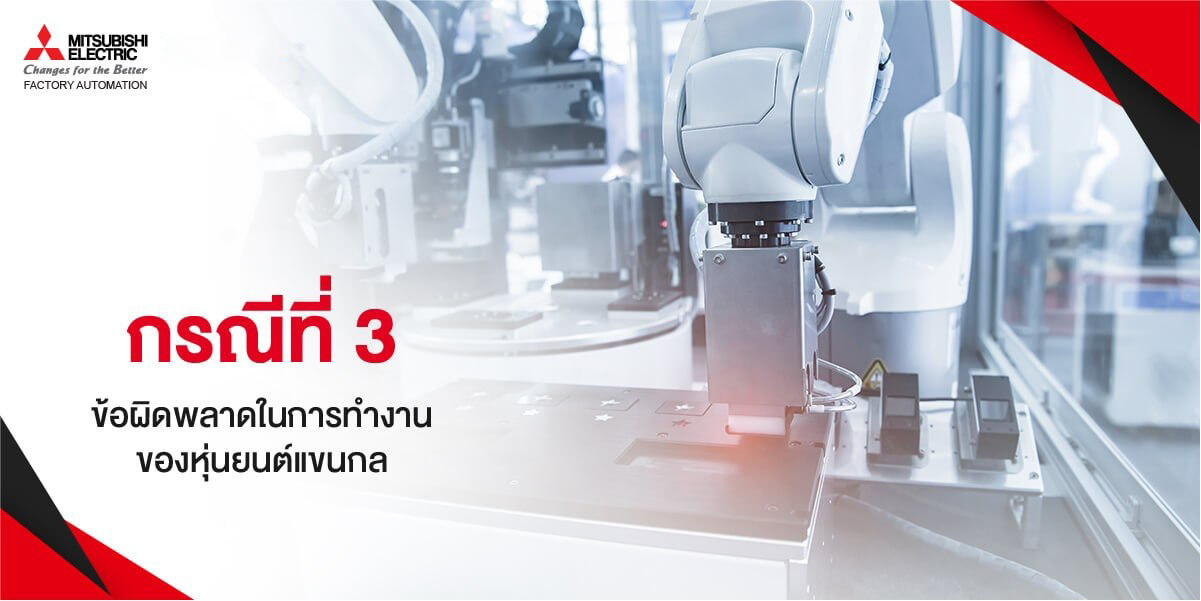
กรณีที่ 3 ข้อผิดพลาดในการทำงานของหุ่นยนต์แขนกล
ปัญหาที่เกิดขึ้นในพื้นที่การผลิต
1. เกิดข้อผิดพลาดในสวิตช์อัตโนมัติของหัวจับอากาศที่หุ่นยนต์แขนกล
2. แม้ว่าจะมีการตรวจสอบสวิตช์อัตโนมัติทั้งหมด แต่ก็กลับมีสถานะปกติและไม่สามารถระบุสาเหตุข้อผิดพลาดได้
3. การตรวจสอบวิดีโอไม่สามารถระบุสาเหตุได้ เนื่องจากไม่ได้บันทึกเงื่อนไขของสวิตช์อัตโนมัติเพิ่มเติมไว้
โซลูชันการจัดการปัญหาในหุ่นยนต์แขนกลด้วยระบบบันทึก (System Recorder)
1. ตรวจสอบรายการที่อาจเป็นสาเหตุของข้อผิดพลาดโดยใช้ฟังก์ชันการวิเคราะห์ข้อมูล (Data Flow Analysis Function)
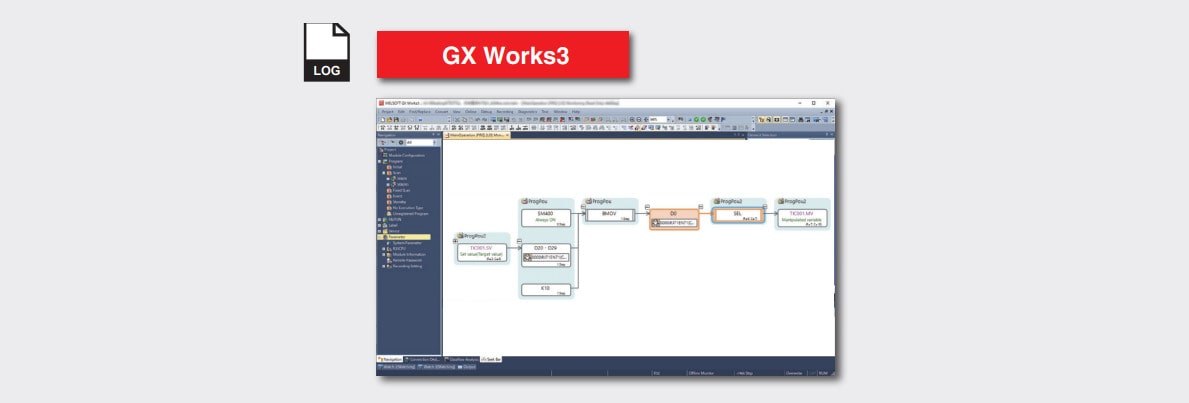
2. เมื่อเกิดข้อผิดพลาดเกิดขึ้นอีกครั้ง ฟังก์ชันการตรวจสอบแบบออฟไลน์ (The Offline Monitoring Function) จะปิดสวิตช์โดยอัตโนมัติ เพื่อหยุดการทำงานของหุ่นยนต์แขนกล
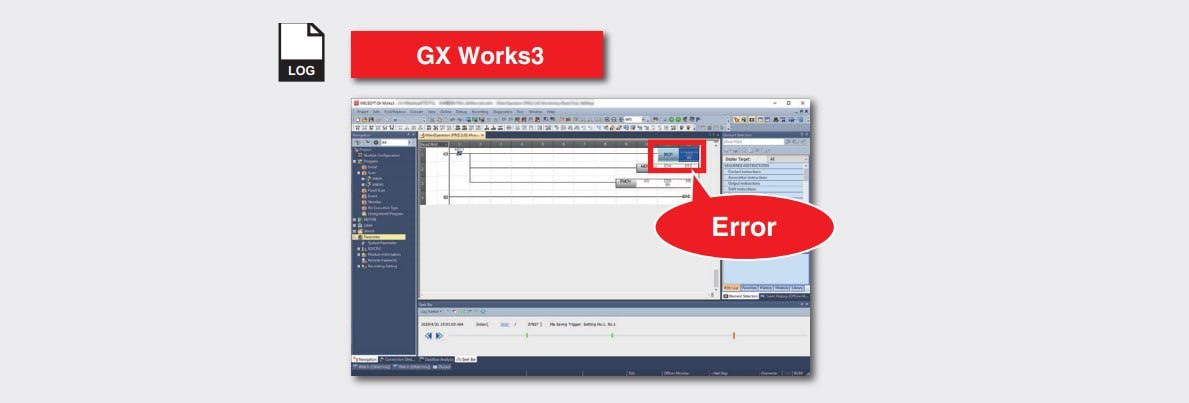
3. สวิตช์อัตโนมัติที่เปิดขึ้นไม่กี่วินาทีหลังจากเกิดข้อผิดพลาด จะสามารถตรวจสอบสภาพของหัวจับที่เกี่ยวข้องใน GX LogViewer ได้ โดยวิเคราะห์จากทริกเกอร์ของสวิตช์อัตโนมัติที่ปิดอยู่ ซึ่งช่วยให้สามารถหลีกเลี่ยงข้อผิดพลาดได้โดยการปรับตำแหน่ง ON ของสวิตช์อัตโนมัติที่ติดอยู่กับหัวจับนั่นเอง
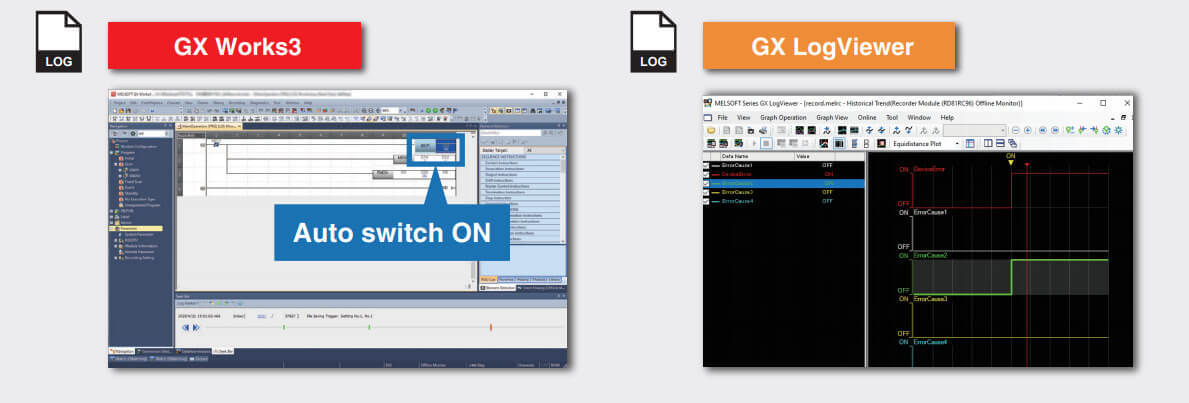
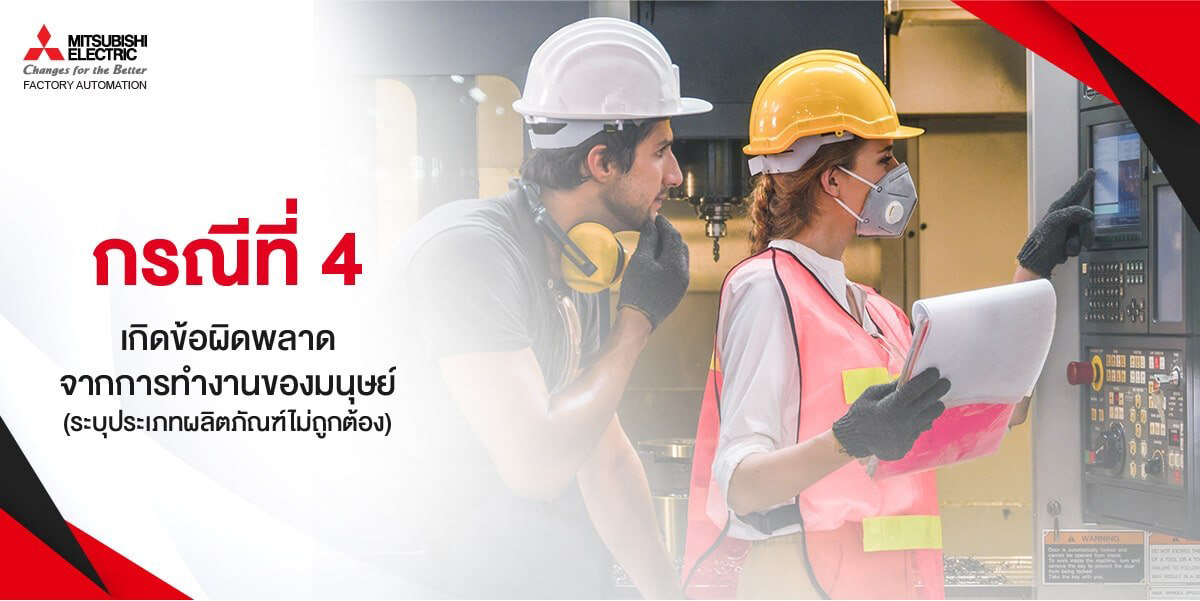
กรณีที่ 4 เกิดข้อผิดพลาดจากการทำงานของมนุษย์ (ระบุประเภทผลิตภัณฑ์ไม่ถูกต้อง)
ปัญหาที่เกิดขึ้นในพื้นที่การผลิต
1. ผู้ปฏิบัติงานป้อนเงื่อนไขการตัดเฉือนชิ้นงานผิดพลาด
2. พบข้อผิดพลาดในการตรวจสอบขั้นสุดท้าย
3. ต้องการเข้าใจรายละเอียดของการดำเนินการที่ผิดพลาด เพื่อเป็นแนวทางในการพิจารณาปรับปรุงแก้ไข
โซลูชันการจัดการปัญหาความผิดพลาดของมนุษย์ด้วยระบบบันทึก (System Recorder)
1. ตรวจสอบประวัติเหตุการณ์ที่บันทึกในซอฟต์แวร์ (Event History) ผ่านซอฟต์แวร์ GX Works3
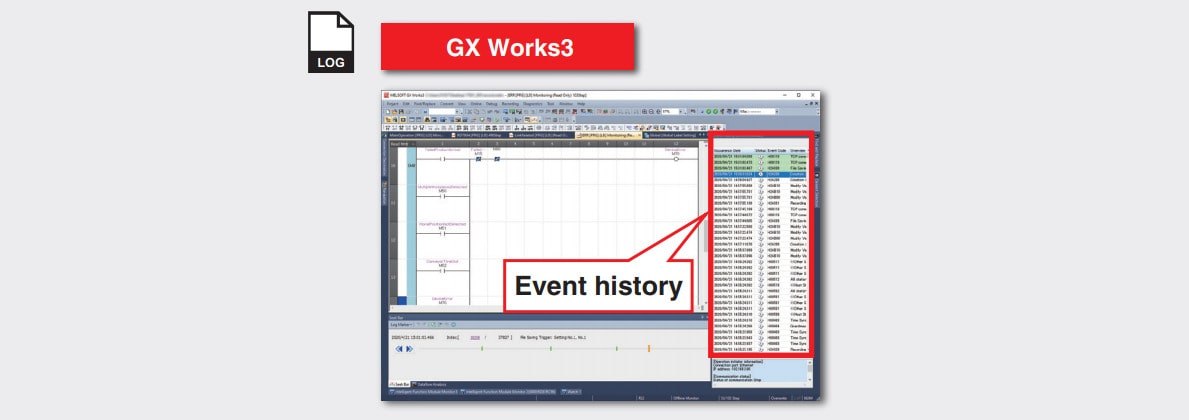
2. ฟังก์ชันการมอนิเตอร์แบบออฟไลน์ (Offline Monitor Function) ของ GOT เชื่อมโยงกับประวัติเหตุการณ์ เพื่อตรวจสอบการทำงานของ GOT อีกครั้ง ด้วยการควบคุมผ่านซอฟต์แวร์ GT Designer3
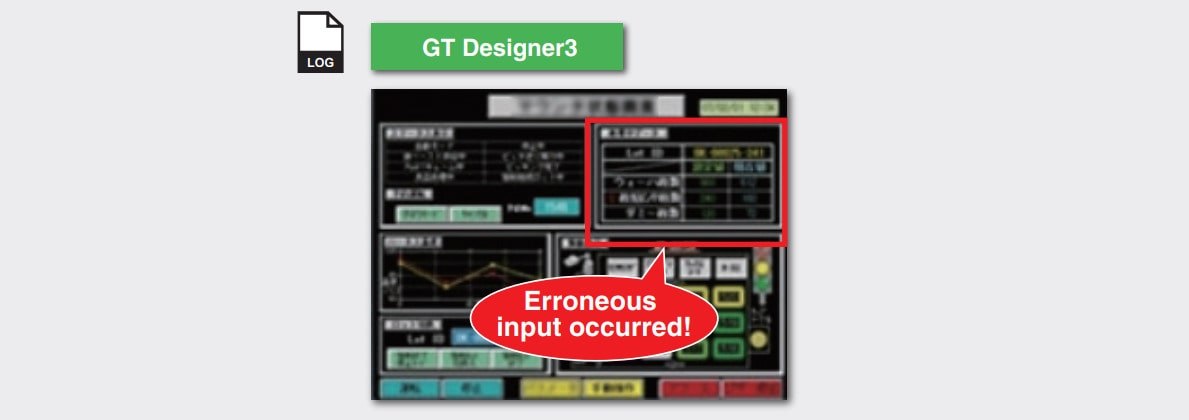
เมื่อข้อผิดพลาดเกิดขึ้นจริงจะพิจารณารายละเอียดการดำเนินการเพื่อป้องกันการเกิดซ้ำ โดยสามารถระบุสาเหตุได้ด้วยระบบบันทึก (System Recorder) และมาตรการป้องกันที่เหมาะสมเพื่อป้องกันการกลับเป็นซ้ำได้
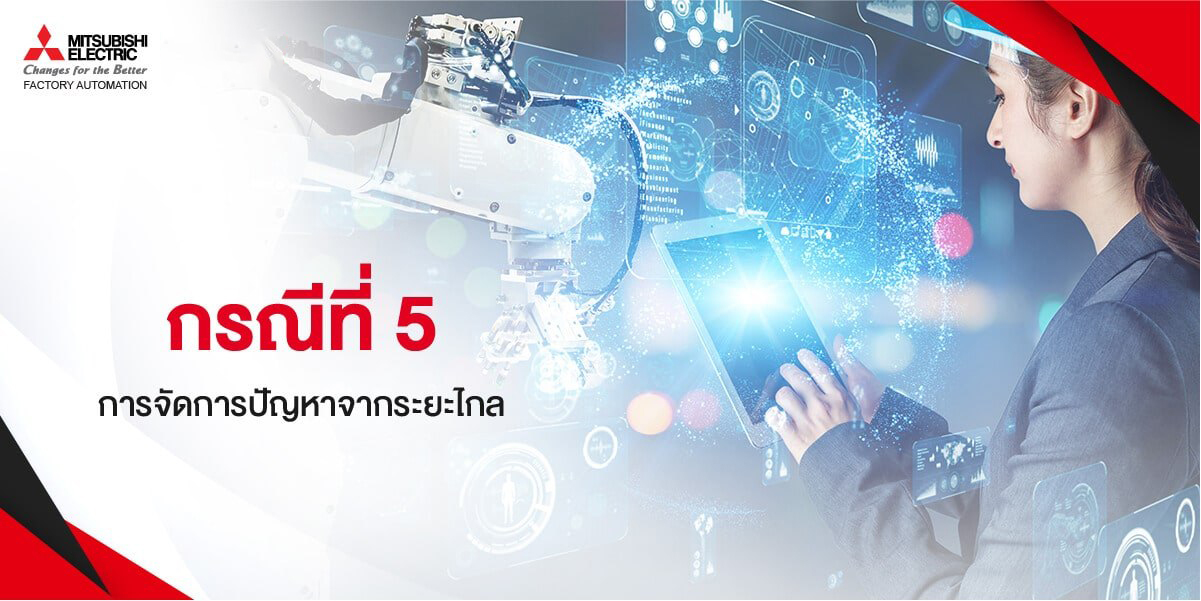
กรณีที่ 5 การจัดการปัญหาจากระยะไกล
ปัญหาที่เกิดขึ้นในพื้นที่การผลิต
1. เกิดปัญหาในไซต์ของสาขาอื่น (ต่างประเทศ)
2. วิศวกรไม่สามารถเข้าใจปัญหาที่เกิดขึ้นบนไซต์ จากการพูดคุยทางโทรศัพท์ได้อย่างถูกต้อง
3. วิศวกรไม่สามารถระบุสาเหตุได้โดยไม่ต้องตรวจสอบฮาร์ดแวร์ ซึ่งการเดินทางเข้าประเทศต้องเสียเวลาและค่าใช้จ่ายจำนวนมาก
โซลูชันการจัดการปัญหาการเข้าไปในพื้นที่การผลิตด้วยระบบบันทึก (System Recorder)
1. ข้อมูลบันทึกและข้อมูลวิดีโอระหว่างเกิดข้อผิดพลาดถูกส่งไปยังสำนักงานในประเทศ
2. วิเคราะห์ข้อมูลด้วยเครื่องมือต่างๆเพื่อระบุจุดที่เกิดข้อผิดพลาด ได้รับการพิจารณาแล้วว่าปัญหานี้เกิดจากปัญหาในโปรแกรมลำดับที่แก้ไขโดยตัวดำเนินการบนไซต์
3. โปรแกรมที่แก้ไขถูกส่งไปยังไซต์ทางอีเมล
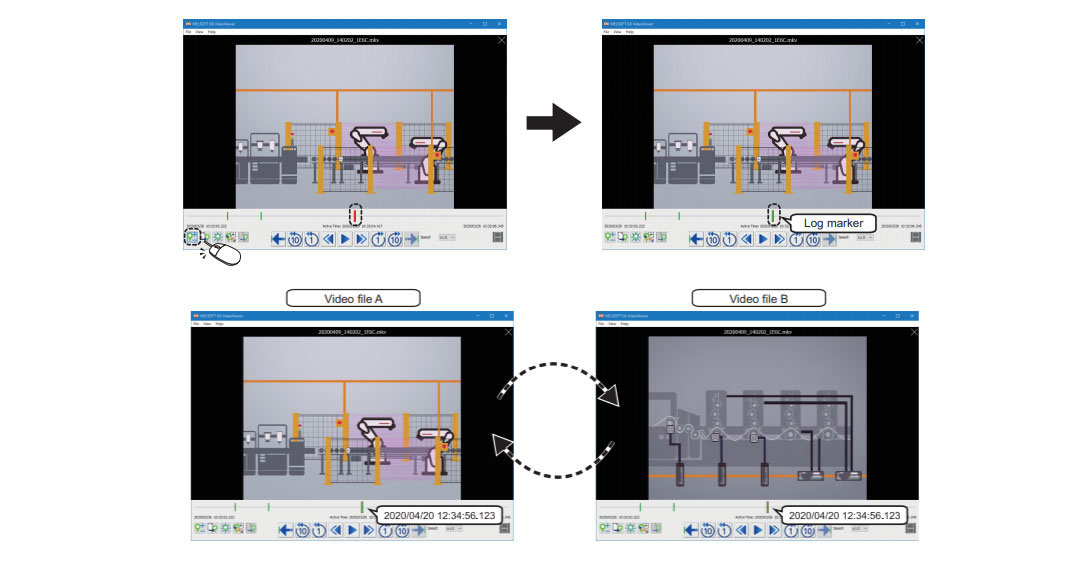