Programmable Controller
MELSEC iQ-R series
Integrated and powerful control for demanding applications.
The MELSEC iQ-R is a full featured control platform with fast processing speeds, network and module synchronization, and multi-discipline control. The advanced design of the MELSEC iQ-R enables users to lead their industries with superior machine performance and productivity. A multitude of CPU and I/O module options make it a flexible solution for a wide variety of applications.
Integrated and powerful control for demanding applications.
The MELSEC iQ-R is a full featured control platform with fast processing speeds, network and module synchronization, and multi-discipline control. The advanced design of the MELSEC iQ-R enables users to lead their industries with superior machine performance and productivity. A multitude of CPU and I/O module options make it a flexible solution for a wide variety of applications.
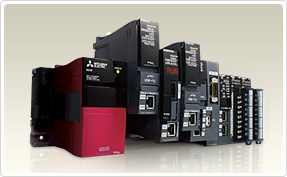
Key Benefits
• 0.98 ns execution speed improves machine response for faster, more accurate applications
• Multi-discipline control with up to 4 CPUs in a single rack and a high speed bus allow for synchronized data communication between process, motion, and sequential control
• GX Works3 programming software with built-in functions and configuration screens reduces development and troubleshooting time
• CC-Link IE Field network with deterministic performance over industrial Ethernet improves machine response and I/O synchronization
• Built-in SD memory card database provides recipe and data logging
functionality without the need for an external server
• Enhanced security features to protect intellectual property as well as plant safety
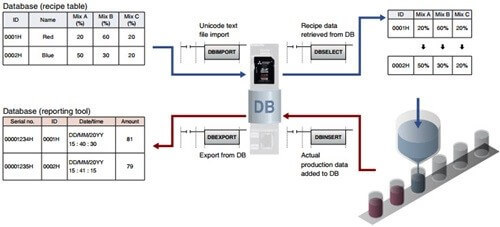
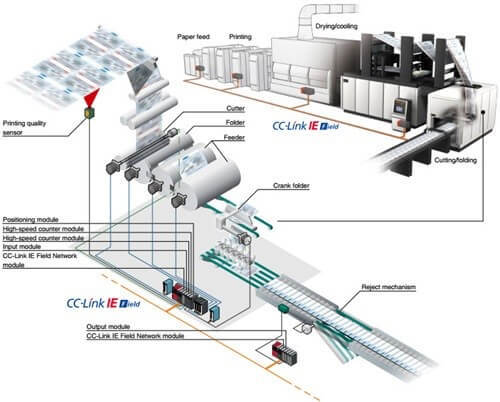
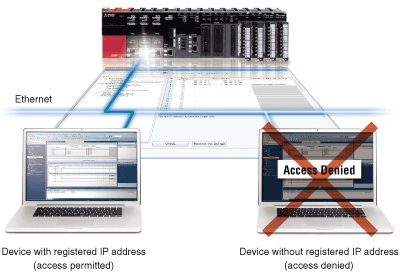
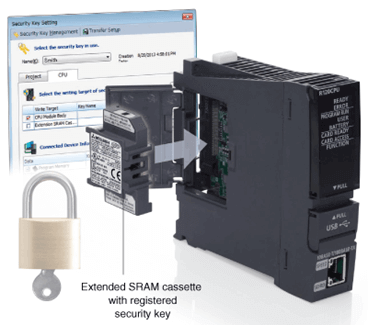
CPU
Programmable automation controllers catering for various different applications.
Base unit
For installing devices such as power supply, CPU and input/output modules. Various base units are available to suit multiple system requirements.
Power supply
This module is used for providing the electrical power for the CPU, input, output, and other modules on the base unit.
I/O module
Devices such as switches, indicator lamps, and sensors can be easily connected to the control system using the digital I/O modules.
Analog I/O module
Analog modules are the main interface between the control process and the automation system, and are specifically designed to interface with sensors that process varying voltage and current signals.
Motion, Positioning, High-speed counter
Distinct set of high-accuracy and fast control response intelligent modules that are ideal for applications requiring high-speed and precision.
Information/network module
This module group enables information exchange with multiple control systems. The module lineup improves production efficiency by collecting and controlling various production information.
Recorder module
The recorder module is a dedicated logging module for system recorder which collects all data per controller scan prior to and after an error event together with a time-stamp.
Lineup |
Programmable
controller CPU: 8 models |
Control method |
Stored program
cyclic operation |
I/O control mode |
Refresh mode |
Programming language |
Ladder diagram |
Engineering
environment |
MELSOFT GX Works3 |
Program size (K
step) |
1200 |
Number of I/O points
[X/Y] (point) |
4096 |
Device/label memory/
standard RAM (K byte) |
3380 |
Data memory/
standard ROM (byte) |
40 M |
Processing speed |
|
LD instruction (ns) |
0.98 |
MOV instruction (ns) |
1.96 |
Floating point addition
(µs) |
0.01 |
Memory interface |
|
Extended SRAM
cassette |
● |
SD memory card |
● |
SRAM card, FLASH
card, ATA card |
— |
External interface |
|
USB |
● |
Ethernet |
● |
RS-232 |
— |
RS-422/485 |
— |
Display unit |
— |
CC-Link IE
connection port |
|
Ethernet |
●*12 |
Network connectivity
(adapter/module) |
|
Ethernet |
● |
CC-Link IE Control |
● |
CC-Link IE Field |
● |
CC-Link |
● |
CC-Link/LT |
— |
SSCNET Ⅲ/H |
● |
AnyWire |
● |
BACnet™ |
● |
MODBUS®/TCP |
● |
MODBUS® |
● |
General
specifications/conformed standards |
|
Operating ambient
temperature |
0...55℃ (60℃*17) |
International safety
standards |
●*18 |
Standard on
corrosive atmosphere |
●*19 |
CE: Council
Directive of the European Communities |
● |
UL: Underwriters
Laboratories Listing |
● |
LR: Lloyd's Register
of Shipping approval |
● |
DNV: Norwegian
Maritime approval |
● |
RINA: Italian
Maritime approval |
● |
NK: ClassNK approval |
● |
ABS: American Bureau
of Shipping approval |
● |
BV: Bureau Veritas
approval |
● |
GL: Germanischer
Lloyd approval |
● |
Key
features/functions |
Line manufacturing |
*1: Supports redundant
system when paired with R6RFM
*2: SFC is not supported in redundant mode and
by safety CPU
*3: Q□UDVCPU only
*4: When using CW Workbench
*5: Does not support QnUDVCPU and certain models
*6: Does not support L02SCPU(-P)
*7: Supports the user Ethernet port of
Q24DHCCPU-V/VG/LS and Q26DHCCPU-LS only
*8: Supports Q□UDE(H)CPU and Q□UDVCPU only
*9: Does not support Q□UDE(H)CPU and Q□UDVCPU
*10: Supports L02SCPU(-P) only
*11: Supports FX3G only
*12: R□ENCPU only
*13: Supports the MELSEC iQ-R Series only.
*14: Supported by expansion board
*15: Does not support Q□(P)(H)CPU and Q□PRHCPU
*16: Supports SSCNET Ⅲ
*17: Only supported when used together with
extended temperature range main/extension base units
*18: R□SFCPU-SET only.
*19: For protection against aggressive
atmosphere and gases, products with a conformal coating (JIS C 60721-3-3/IEC
60721-3-3 Class 3C2) are available on request
*20: Operating ambient temperature from -20℃ is supported by products produced from June
2016 (serial number "166" or later). For details, on supported
products, please refer to the relevant product manual.
Product Comparison
Series |
Modular type |
Modular type |
Baseless type |
|
|
|
|
PAC (Programmable automation controller) |
Programmable controller CPU |
Programmable controller CPU |
|
Lineup |
Programmable
controller CPU: 8 models |
Programmable
controller CPU (Universal model): 25 models |
Programmable
controller CPU |
Control method |
Stored program
cyclic operation |
Stored program
cyclic operation |
Stored program
cyclic operation |
I/O control mode |
Refresh mode |
Refresh mode |
Refresh mode |
Programming language |
Ladder diagram |
Ladder diagram |
Ladder diagram |
Engineering
environment |
MELSOFT GX Works3 |
MELSOFT GX Works2 |
MELSOFT GX Works2 |
Program size (K
step) |
1200 |
1000 |
260 |
Number of I/O points
[X/Y] (point) |
4096 |
4096 |
4096 |
Device/label memory/
standard RAM (K byte) |
3380 |
1792 |
768 |
Data memory/
standard ROM (byte) |
40 M |
16 M |
2 M |
Processing speed |
|||
LD instruction (ns) |
0.98 |
1.9 |
9.5 |
MOV instruction (ns) |
1.96 |
3.9 |
19 |
Floating point
addition (µs) |
0.01 |
0.014 |
0.057 |
Memory interface |
|||
Extended SRAM
cassette |
● |
●*3 |
— |
SD memory card |
● |
●*3 |
●*6 |
SRAM card, FLASH
card, ATA card |
— |
●*5 |
— |
External interface |
|||
USB |
● |
● |
● |
Ethernet |
● |
●*8 |
●*6 |
RS-232 |
— |
●*9 |
●*10 |
RS-422/485 |
— |
— |
— |
Display unit |
— |
— |
● |
CC-Link IE
connection port |
|||
Ethernet |
●*12 |
— |
— |
Network connectivity
(adapter/module) |
|||
Ethernet |
● |
● |
● |
CC-Link IE Control |
● |
● |
— |
CC-Link IE Field |
● |
●*15 |
● |
CC-Link |
● |
● |
● |
CC-Link/LT |
— |
● |
● |
SSCNET Ⅲ/H |
● |
● |
● |
AnyWire |
● |
● |
● |
BACnet™ |
● |
● |
● |
MODBUS®/TCP |
● |
● |
● |
MODBUS® |
● |
● |
● |
General
specifications/conformed standards |
|||
Operating ambient
temperature |
0...55℃ (60℃*17) |
0...55℃ |
0...55℃ |
International safety
standards |
●*18 |
— |
— |
Standard on
corrosive atmosphere |
●*19 |
— |
— |
CE: Council
Directive of the European Communities |
● |
● |
● |
UL: Underwriters Laboratories
Listing |
● |
● |
● |
LR: Lloyd's Register
of Shipping approval |
● |
● |
— |
DNV: Norwegian
Maritime approval |
● |
● |
— |
RINA: Italian
Maritime approval |
● |
● |
— |
NK: ClassNK approval |
● |
● |
— |
ABS: American Bureau
of Shipping approval |
● |
● |
— |
BV: Bureau Veritas approval |
● |
● |
— |
GL: Germanischer
Lloyd approval |
● |
● |
— |
Key
features/functions |
Line manufacturing |
Line manufacturing |
Machine control |
*1: Supports redundant
system when paired with R6RFM
*2: SFC is not supported in redundant mode and
by safety CPU
*3: Q□UDVCPU only
*4: When using CW Workbench
*5: Does not support QnUDVCPU and certain models
*6: Does not support L02SCPU(-P)
*7: Supports the user Ethernet port of
Q24DHCCPU-V/VG/LS and Q26DHCCPU-LS only
*8: Supports Q□UDE(H)CPU and Q□UDVCPU only
*9: Does not support Q□UDE(H)CPU and Q□UDVCPU
*10: Supports L02SCPU(-P) only
*11: Supports FX3G only
*12: R□ENCPU only
*13: Supports the MELSEC iQ-R Series only.
*14: Supported by expansion board
*15: Does not support Q□(P)(H)CPU and Q□PRHCPU
*16: Supports SSCNET Ⅲ
*17: Only supported when used together with
extended temperature range main/extension base units
*18: R□SFCPU-SET only.
*19: For protection against aggressive
atmosphere and gases, products with a conformal coating (JIS C 60721-3-3/IEC
60721-3-3 Class 3C2) are available on request
*20: Operating ambient temperature from -20℃ is supported by products produced from June
2016 (serial number "166" or later). For details, on supported
products, please refer to the relevant product manual.
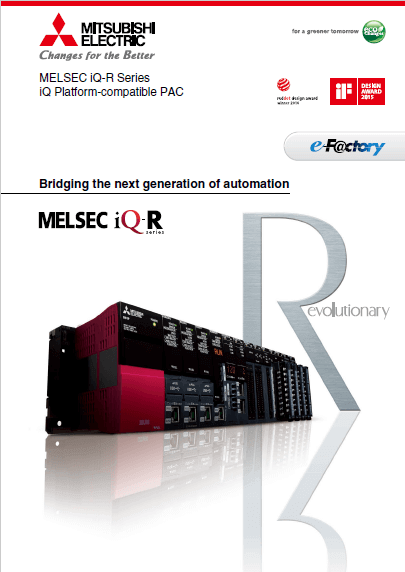
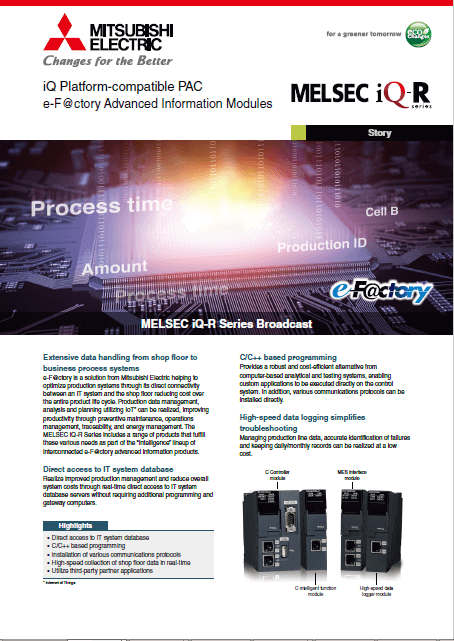
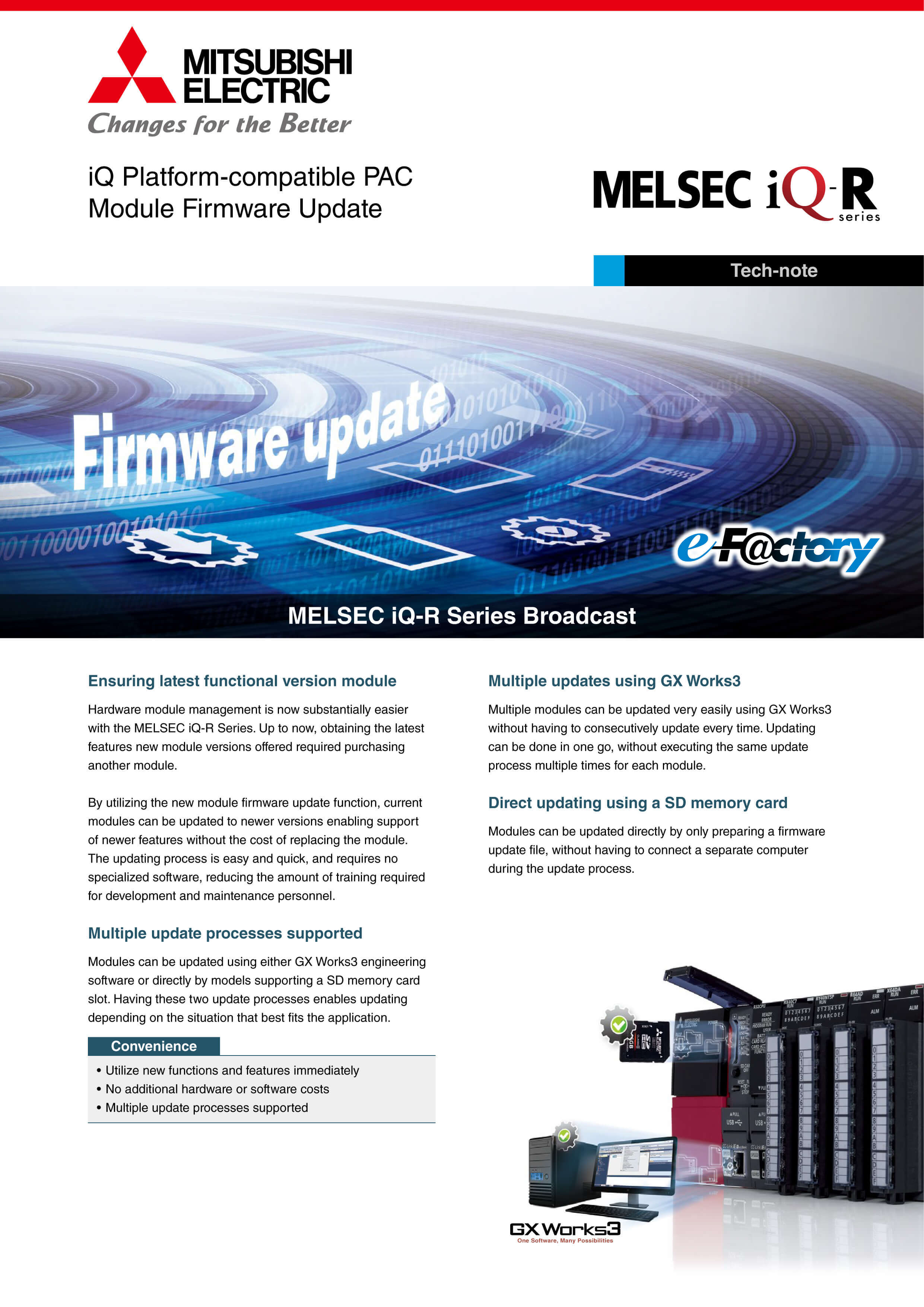